Premium Only Content
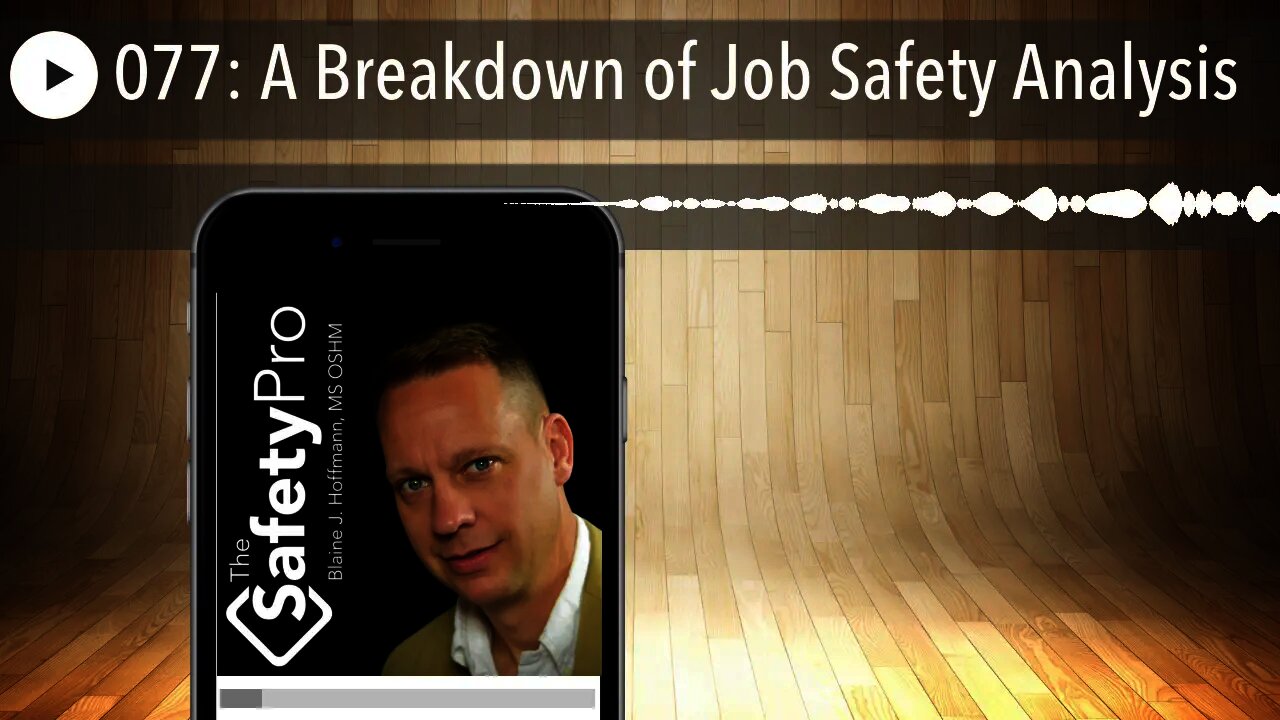
077: A Breakdown of Job Safety Analysis
Subscribe here:
http://www.thesafetypropodcast.com
Powered by iReportSource
Get the JSA template HERE . OSHA has a great page for this topic HERE .
Many companies rely on a super-simple tool to define appropriate safe work practices for specific jobs. The Job Safety Analysis Process (also referred to as a JSA, or Job Hazard Analysis - JHA). The JSA is a very effective means of helping to identify and manage hazards associated with task thus reducing incidents, accidents, and injuries in the workplace. It is also an excellent tool to use during new employee orientations and operator training and can also be used to investigate "near misses" and accidents.
Job Safety Analysis (JSA) is based on the following ideas:
• That a specific job or work assignment can be separated into a series of relatively simple steps.
• That hazards associated with each step can be identified.
• Solutions can be developed to control each hazard.
To start the JSA Process, select the job or task to be performed. Any job that has hazards or potential hazards is a candidate for a JSA. An uncommon or seldom-performed job is also a candidate for a JSA.
Forms or worksheets (see sample worksheet) may vary from company to company but the idea remains the same. Identify all steps, hazards, and safe work procedures before starting the job. I have a template you can download to follow along. It is filled out with a hypothetical job. So grab that and follow along for more context. The JSA process is a multi-step process and goes something like this:
• Basic Job Steps: Break the job into a sequence of steps. Each of the steps should accompany some major task. That task will consist of a series of movements. Look at each series of movements within that basic task.
• Potential Hazards: To complete a JSA effectively, you must identify the hazards or potential hazards associated with each step. Every possible source of energy must be identified. It is very important to look at the entire environment to determine every conceivable hazard that might exist. Hazards contribute to accidents and injuries.
• Recommended Safe Job Procedures: Using the Sequence of Basic Job Steps and Potential Hazards, decide what actions are necessary to eliminate, control, or minimize hazards that could lead to accidents, injuries, damage to the environment, or possible occupational illness. Each safe job procedure or action must correspond to the job steps and identified hazards.
Through this process, you can determine the safest, most efficient way of performing a given job. Thus JSA systematically carries out the basic strategy of accident prevention: The recognition, evaluation, and control of hazards.
Now, how do we document this process and capture the results? It is prepared in a 3-column chart form, either portrait or landscape - I have seen both and listing the basic job steps on the left-hand column and the corresponding hazards in the middle column, with safe procedures for each step on the right-hand column. The right-hand column will essentially become your safe work instructions.
A completed JSA chart can then be used as a training guide for employees; it provides a logical introduction to the work, it’s associated hazards, and the proper and safe procedures to be followed.
For experienced workers, a JSA is reviewed periodically to maintain a safety-awareness on the job and to keep abreast of current safety procedures. The review is also useful for employees assigned new or infrequent tasks.
Let’s talk about how to fill out the JSA. First, there is an art and science to breaking down a job or task into steps. If the steps are too detailed, the JSA will be complicated and difficult to follow. If they are not detailed enough, you may miss important steps and associated hazards. For example, let’s say you are planting a tree, and you need a JSA on how to unload the tree from the truck. You don’t want to say:
Step 1. Remove latch pin from the tailgate
Step 2. Release tailgate latch
Step 3. Lower tailgate to open position
Now you move to planting the tree, let’s say by hand:
Step 1: Retrieve shovel from the back of the truck
Step 2: Place shovel on ground at the specified degree
Step 3: Place dominate foot onto back of shovel at the mid-sole
This is tedious, no one will read that document. Instead, it may be enough to simply say, “open tailgate” as the job step and move to the second part of creating the SJA - listing all the hazards associated with that step. On the flip side, don’t over-simplify it either. For example, when planting the tree:
Step 1: Put tree in ground…that’s it. No step 2.
Ok, an extreme example of over-simplification. But be sure to walk through the job steps and look for opportunities to break it down into steps. If you already have job steps laid out, such as in the case of OEM operating instructions or manual this makes it a bit easier.
To make sure I i
-
Dr Disrespect
9 hours ago🔴LIVE - DR DISRESPECT - WARZONE - SHOTTY BOYS ATTACK
155K23 -
1:30:23
Twins Pod
8 hours agoHe Went From MARCHING With BLM To Shaking Hands With TRUMP! | Twins Pod - Episode 45 - Amir Odom
57.9K18 -
1:02:30
Exploring With Nug
9 hours ago $0.50 earned2 Duck Hunters Missing After Kayak Capsizes!
6.56K -
46:48
Mally_Mouse
3 hours agoLet's Hang!! -- Opening Christmas gifts from YOU!
23.9K -
44:55
Athlete & Artist Show
20 days ago $1.58 earnedNHL 4 Nations Snubs, Was Hawk Tuah Coin A Scam?
32.3K -
33:47
Stephen Gardner
8 hours ago🔥Pentagon Whistleblower UNLEASHES on Biden and Obama!
88.9K145 -
2:20:30
The Dilley Show
10 hours ago $23.94 earnedRoger Stone in Studio plus Q&A Friday! w/Author Brenden Dilley 12/27/2024
75.8K16 -
1:57:02
The Charlie Kirk Show
8 hours agoThe Great H-1B Battle + AMA | Lomez | 12.27.24
155K208 -
11:39
Russell Brand
1 day agoWhat You're Not Being Told About The Syrian War
161K241 -
DVR
Bannons War Room
1 year agoWarRoom Live
101M