Premium Only Content
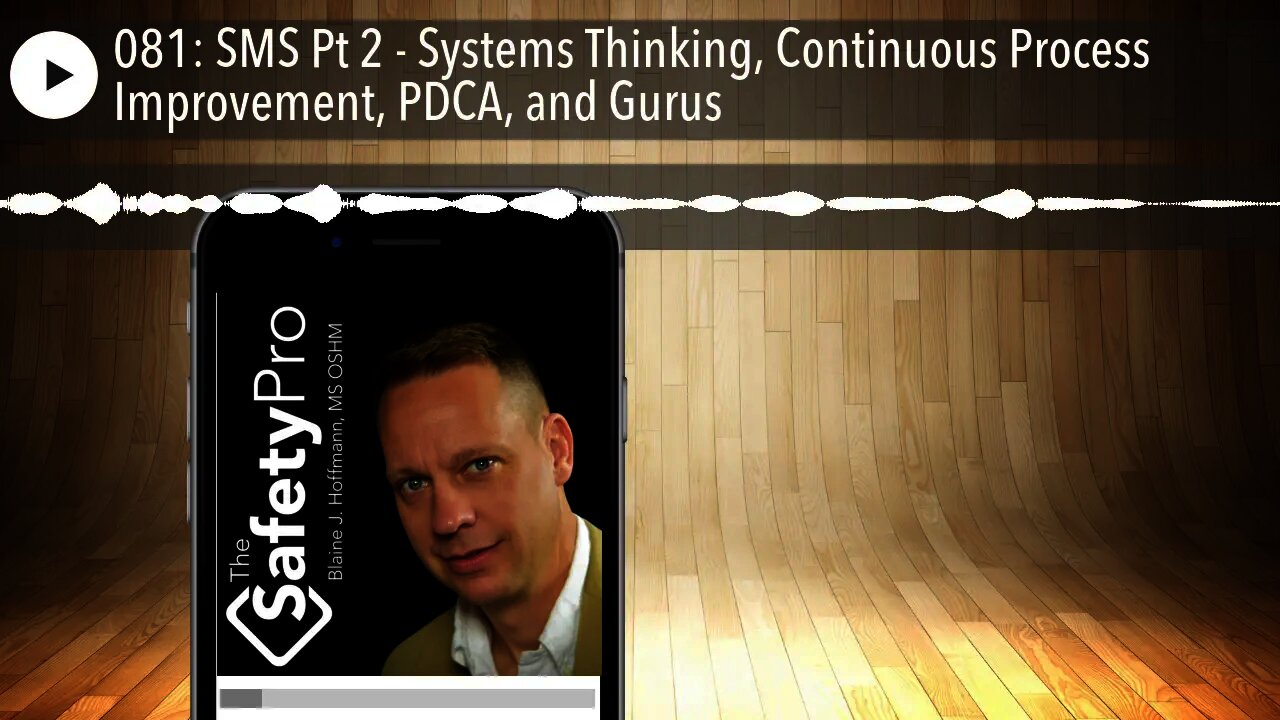
081: SMS Pt 2 - Systems Thinking, Continuous Process Improvement, PDCA, and Gurus
Subscribe here:
http://www.thesafetypropodcast.com
Powered by iReportSource
In this episode, I continue my series breaking down Safety Management Systems (SMS) and will talk about Continuous Process Improvement. Before I can do that, we need to understand something else about SMS - In episode 80 of The SafetyPro Podcast , Safety Management System (SMS) Defined, I talked about how you need to move away from individual programs and toward a systems approach to safety management. Well, there is something called systems thinking, and we are going to get into what that is and how you can shift not only the way you look at managing safety but also how your organization can make the shift from managing programs to integrating safety within the rest of the business by using systems thinking.
I recently came across an interesting article over at The Systems Thinker written by Micheal Goodman , and I thought it would help safety pros better understand what system thinking is all about. Michael is an internationally recognized speaker, author, and practitioner in the fields of Systems Thinking, Organizational Learning, and Leadership. The article is called SYSTEMS THINKING: WHAT, WHY, WHEN, WHERE, AND HOW? He writes:
"The discipline of systems thinking is more than just a collection of tools and methods – it's also an underlying philosophy. Many beginners are attracted to the tools, such as causal loop diagrams, in hopes that these tools will help them deal with persistent business problems. But systems thinking is also a sensitivity to the circular nature of the world we live in; an awareness of the role of structure in creating the conditions we face; a recognition that there are powerful laws of systems operating that we are unaware of; a realization that there are consequences to our actions to which we are oblivious.
Systems thinking is also a diagnostic tool. As in the medical field, effective treatment follows a thorough diagnosis. In this sense, systems thinking is a disciplined approach for examining problems more completely and accurately before acting. It allows us to ask better questions before jumping to conclusions.
Systems thinking involves moving from observing events or data, to identifying patterns of behavior over time, to surfacing the underlying structures that drive those events and patterns."
So you can see how this sets us up for moving away from merely managing programs toward a systems approach to safety. We need to understand the relationships the individual safety programs have with other areas of the business - how people think, feel, and behave when interacting with them.
It is also essential to understand that when we use the term system, it implies that the entire business is a single system and composed of many related subsystems. An accident occurs when a human or a mechanical part or multiple parts of the system fails or even just malfunctions. The system safety approach reviews the accident to determine how and why it occurred and what steps could be taken to prevent a recurrence. The goal of a systems approach is to produce, you guessed it, a safer system.
Therefore, at a minimum, a safety system is a formal approach to eliminate or control hazardous events through engineering, design, education, management policy, and supervisory oversight and control of conditions (environment) and practices, the organizational policies, practices, and overall organizational culture, etc. Notice I included the human and organizational aspects? Yes, traditional systems safety does address these areas.
In episode 80 of this podcast, I also talked about how SMS is a continuous improvement process that reduces hazards and prevents accidents. So what is a Continuous Improvement Process exactly? And how does it help us improve safety? Simply put, it is an ongoing effort to improve products, services, or processes. Or put another way; a recurring activity or activities to enhance performance. Typically, the goal is for "incremental" improvement over time and, in some cases, significant improvements all at once.
So once again, I will use Lean principles to explain this concept. First, I want to start with some structure, which will lead to this concept of continuous improvement. There is a term known to Lean practitioners; Kaizen. The Japanese word kaizen simply means "change for better" and refers to any improvement, either a one-time deal or a continuous process, either large or small, in the same sense as the English word "improvement." So when you hear the phrase "Kaizen Event" - that simply means an improvement event.
The most well-known example of a Kaizen approach is the Toyota Production System, or TPS, where everyone is expected to stop their moving production line in case of any abnormality and, along with their supervisor, suggest an improvement to resolve the abnormal issue. This will initiate a cycle of activity aimed at not merely fixing that one
-
4:07:42
Alex Zedra
17 hours agoLIVE! Scary Games with the Girls
164K6 -
22:35
DeVory Darkins
14 hours ago $27.93 earned"Don't Call Me Stupid!" Election Guru HUMILIATED by Left Wing Host
73.6K76 -
1:41:14
Megyn Kelly
15 hours agoMace's Quest to Protect Women's Spaces, and RFK vs. Media and Swamp, w/ Casey Means and Vinay Prasad
83.4K116 -
5:08:25
Drew Hernandez
12 hours agoLAKEN RILEY'S KILLER CONVICTED & GIVEN LIFE IN PRISON
65.6K83 -
59:31
Man in America
17 hours agoEven WW3 Can't Stop What's Coming—the Cabal is COLLAPSING w/ Todd Callender
126K84 -
3:51:28
I_Came_With_Fire_Podcast
17 hours agoSPECIAL LIVE FIRE w/ Bearded Viking Mead Co
93.3K9 -
1:28:52
Kim Iversen
15 hours agoUnmasking the Truth: Most Censored Historian On Past Election Meddling, COVID, and Trump
88.7K96 -
2:10:00
TheSaltyCracker
13 hours agoNow Lefties Lose Bathroom War ReeEEeE Stream 11-20-24
163K470 -
1:03:31
Fresh and Fit
15 hours agoWhy Men Need Options To Avoid Falling For This!
127K19 -
1:26:56
Flyover Conservatives
1 day agoWar Raging, Bank Closing, and Humanoid Robots: It’s Biblical! - Clay Clark | FOC Show
61.2K21