Premium Only Content
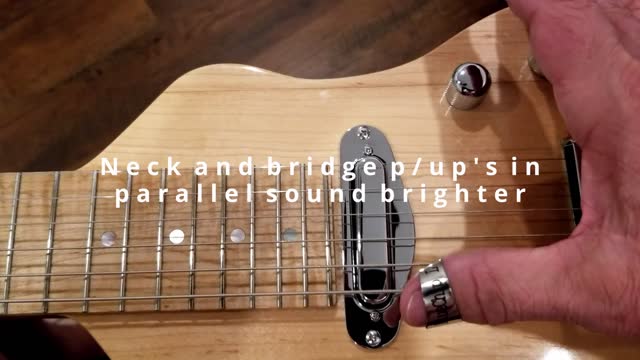
My DIY Homemade Lap Steel Guitar
My DIY Homemade Lap Steel Guitar - 'Blondie'
Solid Maple body
Maple fretboard
Fender Telecaster saddle bridge with chrome 'Ashtray' cover
Fender chrome neck pickup mounting ring
Fender chrome output jack
Stewart Macdonald medium frets
Stewart Macdonald pearl fret dots
Stewart Macdonald chrome string ferrules
Gotoh chrome tuning machines
Gotoh chrome volume, tone and switch control knobs
Seymour Duncan STL-2 'Hot for Tele' bridge pickup
Seymour Duncan STR-2 'Hot for Tele' neck pickup with chrome cover
Alpha 'make before break' 3 pole, 4 position pickup switch
Pos. 1 - Bridge pickup only
Pos. 2 - Bridge and neck pickups in series
Pos. 3 - Bridge and neck pickups in parallel
Pos. 4 - Neck pickup only
A-250K dual volume and tone control pot, w/.047 uf tone capacitor
D'Addario Nickel Steel custom string set from Troy Brenningmeyer
Tuned to Open 'D' - D A D F# A D
I made this lap steel based on the design by Martin Koch
using his book "Build you own Lap Steel" at
http://www.BuildYourGuitar.com/lapsteel
I applied a Birchwood Casey Tru Oil hand rubbed finish - after cutting the shape of the guitar, I sanded with 80 through 2000 grit sandpaper to get the final shape and smoothness. I then drilled the holes and pockets with a Forstner bit then used a Dremel to smooth the pockets out. I dampened the body in between sandpaper grits a few times to raise the grain for sanding. Sanding is critical before applying the Tru Oil finish. All scratches have to be removed otherwise they will get amplified by the oil finish. Wetting the body with a damp sponge helps see the scratches and raises the wood grain prior to finishing. Using a bright light makes the scratches easier to see.
I then applied six very thin base coats of Tru Oil with a lint free cloth. Then, I flattened the finish with 600 grit wet dry sandpaper and mineral spirits to fill the grain. I then applied a few more coats and sanded with 600 again, and 800 on the end grain.
I then grain filled again using the slurry method using 1000 wet/dry paper on the back of a large pencil eraser for a sanding block. I sanded with the grain using Tru Oil mixed 50-50 with either mineral spirits or Naphtha as a lubricant, no water! After that, I applied 4-5 more coats of Tru Oil then flattened it with 0000 steel wool. Always sand gently and with the grain. You have to flatten the finish as you go...every 4 or 5 coats, flatten the finish down with 0000 steel wool.
I used the same flattening method after applying Tru Oil diluted half and half with Naphtha every 4-6 coats thereafter. For maximum gloss, reduce the Tru Oil 50% with naphtha or mineral spirits when applying the coats. This reduces streaking from the applicator also. Allow 12-24 hours between applying the layers and every 3 or 6 layers, go back to sanding/flattening.
For building up coats, I did 2 or 3 light coats a day wiped with the direction of the grain. Lay it down with full, long strokes and then dry a couple of hours before the next coat depending on the temperature/humidity. Hint: Use another small sanded piece of wood to apply the Tru Oil at the same time you apply it to the guitar. You'll be able to use that piece to gauge the drying times without risking touching and fingerprinting the guitar. When applying the coats, don't try and take all of the oil off and absolutely do not work it to the point of it becoming sticky. If it gets sticky, stop! Level as you apply more coats.
The trick is to apply the Tru Oil VERY THIN! I tightly balled up 1/2 of a paper towel, dipped it in Tru Oil and then placed it in a lint free cloth as an applicator and rubbed it in. A little goes a long way!
I even sanded the finish as I applied more coats pretty aggressively with 2000, up to 3000 wet dry sandpaper using a pink eraser as a sanding block, and it made an even better finish than the steel wool. It was really at 2000 grit and up where there was a change in luster, from what I would say a satin finish to a low gloss. Again, the key here is thin, light coats. Avoid the temptation to lay the Tru Oil on thick.
The great thing about Tru Oil is that you really just keep going until either your arm feels like its going to fall off, or you've got the appearance you want. I wanted glossy. Remember, very thin and numerous coats work best. When building coats, you also want to lay it down wet. Not so wet that it runs or leaves ridges, but wet and glossy looking. If you put it on too thick, don't worry. It'll level out a bit if you dilute it with mineral spirits or Naphtha and you can sand and polish it smooth after that coat dries. After 14-16 coats of Tru Oil and drying for a week, I buffed it with cotton and polished it with a high quality paste wax.
I was going to put a cream or pearloid binding on the fretboard edge but decided not to in the end. Ultimately, it was a very rewarding project and overall I'm very happy with how my first lap steel build turned out. And, it has unbelievable sustain and sounds fantastic!
-
0:59
Kids Vids
3 years ago $0.02 earnedHomemade Lap Steel Guitar
927 -
0:57
TIMOTHYP3TTIT
3 years agoHomemade DIY Chicken Feeder
441 -
0:10
StretchHealing123
4 years ago $0.06 earnedHomemade Homemade Homemade Homemade
5751 -
34:43
Stephen Gardner
3 hours ago🚨Trump Lawyer makes TWO HUGE ANNOUNCEMENTS | Benny Johnson
26.9K20 -
2:17:31
Robert Gouveia
4 hours agoJudge BLOCKS Proof-of-Citizenship! Trump BACK to Supreme Court! Deportee Discovery STAYED!
36.5K16 -
LIVE
MyronGainesX
18 hours ago $11.24 earnedCollege Debate Reaction, Jordan Peterson Sells Out, Shannon Sharpe Shakedown!
2,134 watching -
LIVE
Lilpaul112
3 hours agoSolos On the Island / Repo Time With the Brrrap Pack Gang!
134 watching -
1:33:35
theoriginalmarkz
3 hours agoEvening News with MarkZ, joined by Jonathan Otto. 04/24/2025
40.9K3 -
LIVE
GrimmHollywood
3 hours ago🔴LIVE • GRIMM HOLLYWOOD • REPO with the BRRRAP PACK • THEIR FIRST TIME PLAYING •
46 watching -
10:10
Mrgunsngear
3 hours ago $1.07 earnedNew Trijicon MRO SD - The Best American Made Red Dot Optic?
19.8K3