Premium Only Content
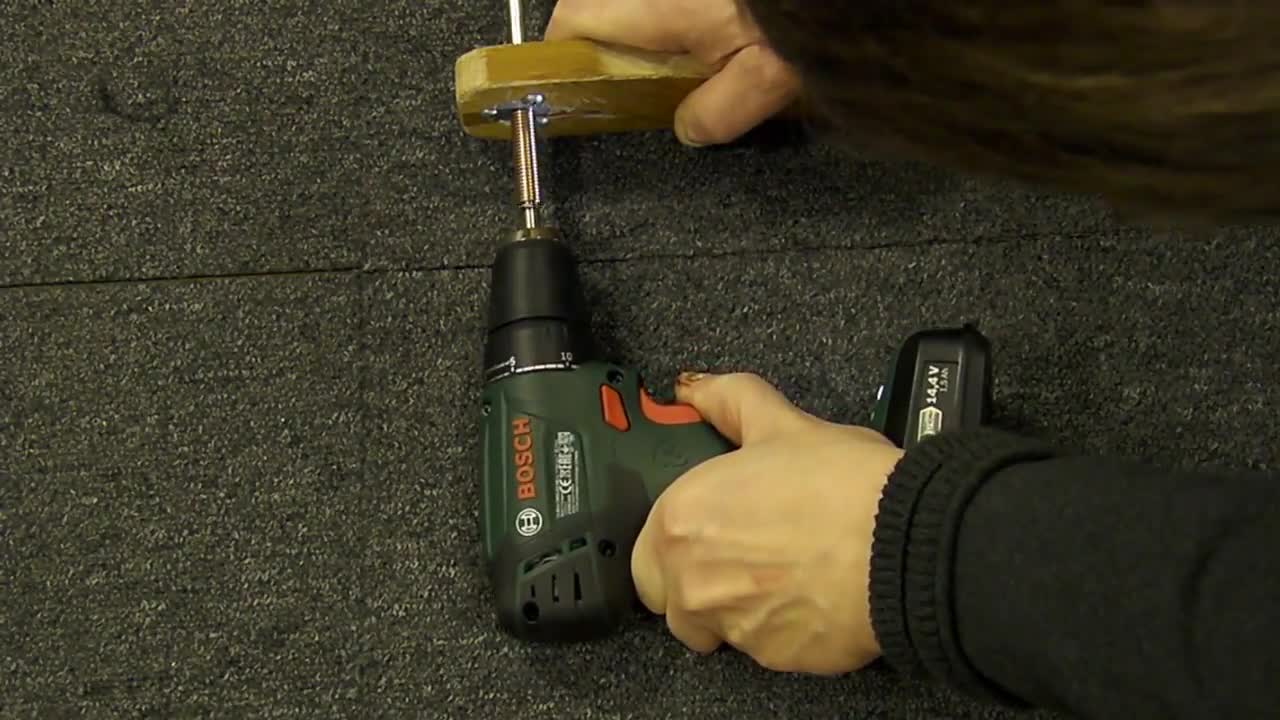
Making a Coil to Cut Rings from for Chainmail
Here I am showing you my little gadget which I use to make my coils of wire. The wire used is 1,6 mm (14 AWG) SG-2 MIG Welding wire (your box standard / garden variety welding wire for welding low alloy steels)
I use this wire, which is the same diameter and roughly the same properties as the (in home chain mail making) commonly used electric fencing wire. This wire is the thickest available on a spool, in this case a 15 kg (about 32 lbs).
Yes I DID cut myself on a piece of wire which protruded from the jig. You have to be VERY careful of what you are doing with wire spools and cut ends flapping about or rotating in the jig because wire will mess you up in a second. I cut my thumb and I believe I was lucky this time and I could get away with a large band aid and some disinfectant. Luckily I have all my shots in order...
I recommend you have some system in place in which the spool (large or small) of wire can be held and it's perks kept in check because wire spools tend to unwind violently if not mounted/handled correctly. I will place my spool in a crate or a strong enclosure and I will most likely have to add some sort of wire break (just a piece of left over oak with a hole drilled into it) to prevent unwinding when the tension is released when the coil are removed from the rod and a new coil is being started.
This coiling aid and the power drill makes a 1 foot long coil in about 20-30 second, provided the spool is rotating freely and no messy unwinding of the main spool is going on. The coil contains about 210 rings which weigh in at about 104 grams.
The wire comes in the tool (from the spool, which has it's own anti recoil brake on it (two piece of wood which get pressed together by two springs) and has to pas throught the handle of the tool. The wire passes through one drilled hole, exits on the top of the tool and enters into the tool again at a slight angle (maybe 20-25 degrees) The wire exits the tool again facing the coiling die, which is a 8 mm steel rod salvaged from an old printer. The wire is fed through a hole drilled into the rod and is guided by a cut open large fender washer onto the die. The washer ensures pressure is exerted laterally to the coils edge to make sure the coil is wound neat and tight, ensuring a nice an even coil which in turn make very nice rings.
I recommend you use either a powerful drill (maybe a drill press which let's you change the speed and torque) or a small lathe if you are doing this coiling in large quantities. The stresses on the power tool are quite significant and most likely cheaper or the more lighter power tools will get very hot very fast and most likely will fail (burn out or simply develop a mechanical issue)
Best option would most likely be to make a coiling machine purposely for the job.
Hope you enjoy the (short) video.
-
5:23
kimberlyhilligoss
4 years agoMaking a gravy boat from a slab.
37 -
0:40
ksevers
4 years agoMaking Tomatoe sauce from garden.
59 -
10:53
metal working and casting
4 years ago $0.02 earnedFoundry Pattern Making from Parts
170 -
1:55
christianbushnell
4 years ago $0.01 earnedMaking 1 million dollars from scratch! ep1
334 -
0:21
osharp
4 years agoMaking fun from piano , thumbs up?
109 -
4:33
Nighthawk Creations
4 years agoMaking a Swan
736 -
0:14
JensTommy666
4 years ago $0.04 earnedMaking lunch.
174 -
1:05
brentaurban
4 years ago $0.04 earnedMaking lumber
274 -
0:37
AdventureNow
4 years ago $0.01 earnedMaking waffles
831 -
5:00
William Hall
4 years agoRobinhood STOPS The Poor From Making Money Off The Rich
1103