Premium Only Content
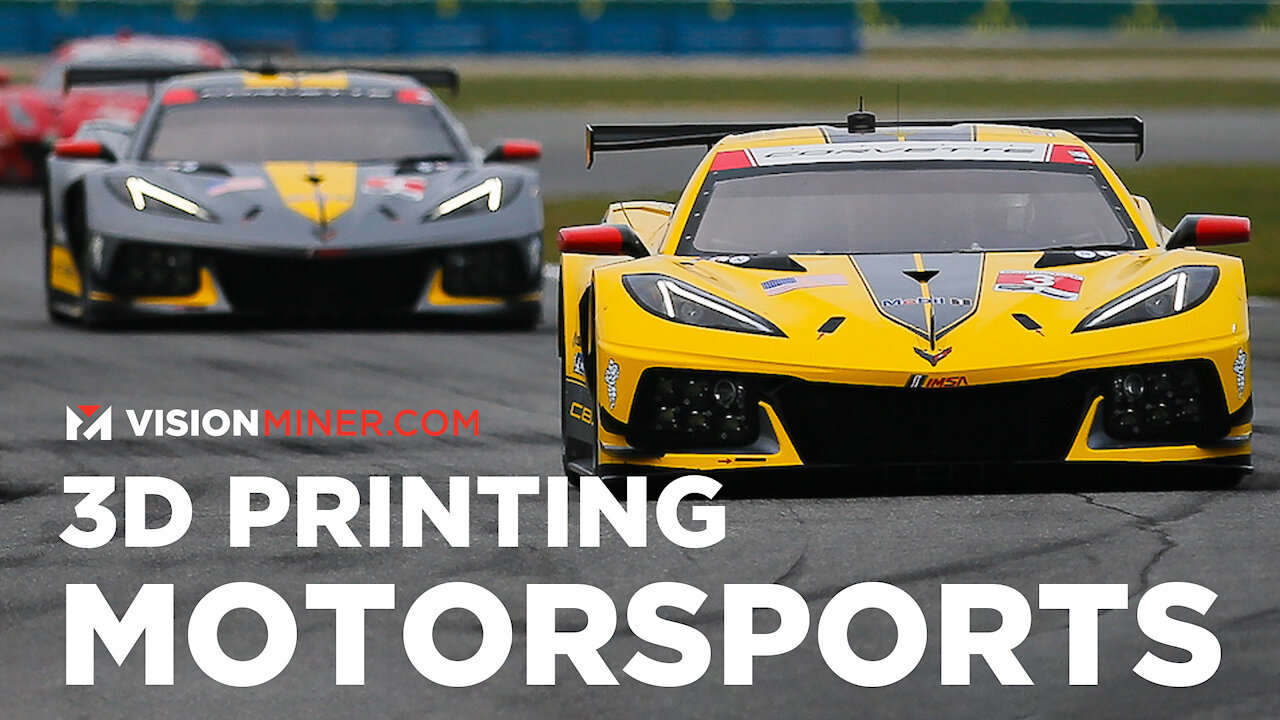
3D Printing In Racing! Toyota, McLaren, Chevrolet, BMW Using 3D Printing To Win!
3D and Motorsports. High performance materials and manufacturing meet one of the toughest proving grounds for engineering. Mechanical stresses, chemicals, extreme heat, high g forces, etc.
In the 2020 season, Chevrolet race cars covered 80,000 miles with hundreds of 3D printed parts and earned numerous class victories. Starting with Chevy’s latest race car the corvette C8.R which made its race debut back in January at the Rolex 24 at Daytona equipped with 75 3D Printed parts including the oil tank, tank inlet and cap, air conditioning driver cooling box and integrated hydration system, power steering pump bracket and headlight assemblies. 50 of these parts were designed or printed in house by General Motors. The two C8.R’s have been driven close to 8,000 miles across 10 races this year. Corvette Racing has brought home 6 victories this year, 3 1-2 finishes and both the driver’s and manufacturer’s championships. In IndyCar, Chevrolet has taken additive manufacturing further, creating parts for their Indy V6 engine. Components in the exhaust system are 3D printed to help eliminate failure points caused by traditional manufacturing. This not only improves upon reliability but also gives the benefit of increased design flexibility and freedom while reducing costs. Chevrolet powered IndyCars have run over 60,000 miles since the beginning of the 2020 season. For the 2020 NASCAR Cup Series, Chevrolet introduced the Camaro ZL1 1LE replacing the Camaro ZL1. This new iteration made use of over 500 3D-printed prototype parts to develop the new ZL1 1LE body in the wind tunnel. In addition, the Camaro ZL1 1LE uses a 3D-printed gear cooling duct that has accumulated nearly 18,500 miles of competition in 27 races.
Toyota entered a partnership with 3D Systems in August of last year with the goal of developing first-to-market manufacturing solutions including 3D printers, materials and software with the goal of advancing automotive design and production. They aim to demonstrate how additive manufacturing solutions can positively impact and even transform the competitive industry that is motorsport. TMG has chosen 3D Systems for this partnership because they share our pioneering spirit—exhibited by the fact that they introduced the world to 3D printing. We see the unparalleled potential of combining 3D Systems’ expertise and know-how with that of TMG to create technologies and define new additive manufacturing innovations in the automotive industry.”
McLaren Racing is one of the most revered names in all of motorsport as one of the most successful teams of all time. In 2017, McLaren Racing and Stratasys announced a partnership similar to the partnership we just discussed. McLaren Racing and Stratasys have been in a 4 year partnership with the latter being the Official Supplier of 3D Printing solutions to the McLaren Racing Formula 1 team and provide the team with additive manufacturing and 3D Printing solutions. The company will assist the team in increasing its capacity for rapid manufacturing at the McLaren Technology Center in Woking, UK. McLaren has been utilizing additive manufacturing to speed up car development across the board. From tools, and parts that go on the car itself like hydraulic brackets in carbon fiber nylon. Parts like these can even be printed trackside so spares and new iterations can be created in just a few hours.
Finally we have BMW more specifically their Motorrad Motorsport division that races in FIM Superbike with the S1000RR motorbike. When BMW engineers identify a component for improvement, prototypes are printed in plastic and their function and ease-of-installation are checked on the bike. As soon as a part is perfect, the final data is sent back to the Munich AM facility, which then manufactures it for competitive racing in metal or carbon. For smaller components or spare parts that need to be manufactured that aren’t subject to extreme stress, such as sensor holders and quick-release couplings, the complete process takes place on-site with the 3D printer. BMW has used its on-site additive manufacturing process to optimize bike parts, including brake ventilation systems in plastics reinforced with carbon fiber, complex molded parts, titanium crash pads, aluminum distributor boxes, and aerodynamic trim parts.
Let us know if you liked this video by leaving a like and comment down below.
At Vision Miner, we specialize in Functional 3D printing, especially high-performance plastics like PEEK, ULTEM, PPSU, PPS, CFPA, and more. If you're interested in using functional 3D printing and materials in your business, feel free to reach out, and we can help you make the right choice for your application.
Call 833-774-6863 or email contact@visionminer.com, and we're here to help!
Follow Us
►Facebook: https://www.facebook.com/visionminer/
►Instagram: https://www.instagram.com/visionminer/
►Twitter: https://twitter.com/visionminer
-
3:56
Vision Miner 3D Printing
4 years ago $0.02 earnedUL Blue Card Plastics for Additive Manufacturing / 3D Printer Filament - What does it mean?
186 -
1:06
Oscar Steele & Company
4 years ago $0.01 earned3D Printing FLSUN QQ-S
87 -
0:36
alexb714
4 years ago3D Printing 1.1
154 -
4:04
TheSim Art
4 years agoComplete Baby Yoda 3D Printing
88 -
7:53
Quentin's Videos on Printing and more
4 years ago $0.01 earned3 D printing software
94 -
6:41
Katbox3Dprinting
4 years agoKatBox 3D printing
251 -
3:29
PROJECT NEET PRINTS
4 years ago $0.01 earned6 color separation printing
126 -
0:32
SenseiMitch
4 years ago $0.01 earned3D printing a birdhouse
442 -
0:15
JoeV64
4 years ago3d Printing Communication Tower Model 2
54 -
0:21
JoeV64
4 years ago3D Printing Headset clamp
53