Premium Only Content
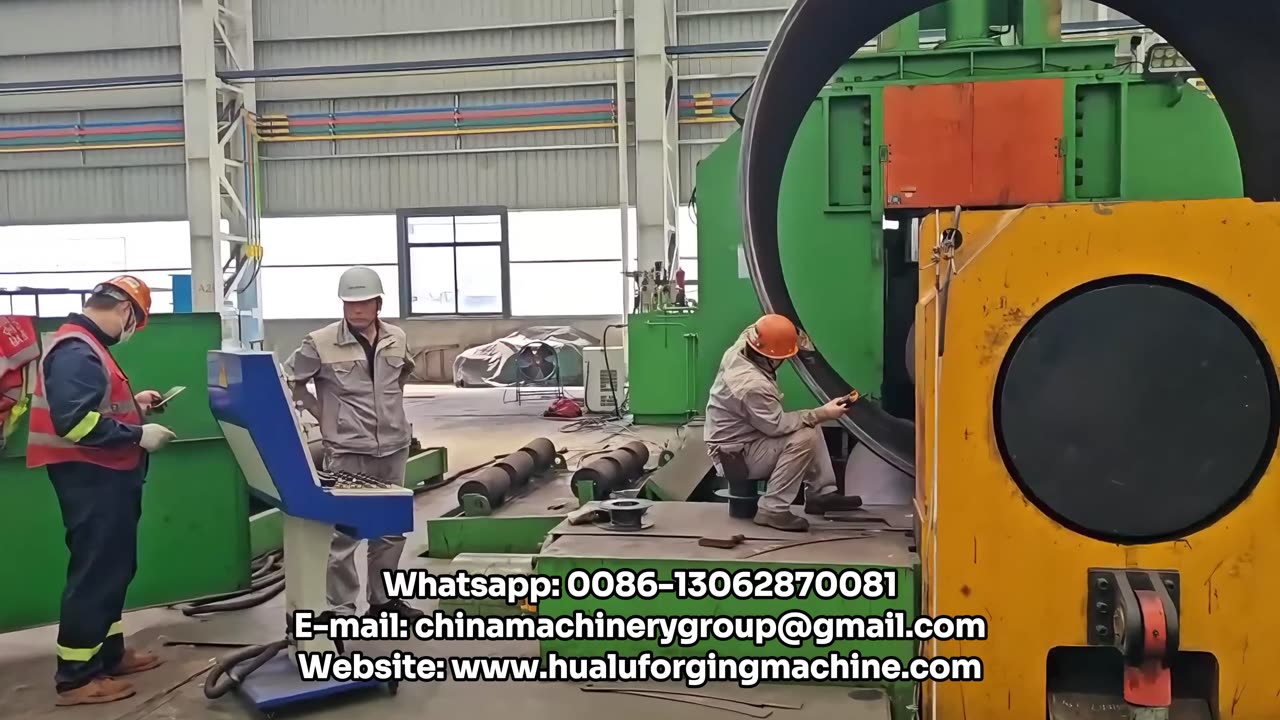
3 roll plate bending machine installation video
3 roll plate bending machine installation video; Installing a 3-roll plate bending machine requires careful planning, precise execution, and thorough understanding of mechanical principles. This comprehensive guide will walk you through the essential steps and considerations for a successful installation.
Pre-Installation Planning
Understanding the foundational requirements is crucial for any successful machine installation. Key considerations include:
- Site preparation and assessment
- Power supply requirements
- Foundation specifications
- Space requirements and clearances
- Environmental conditions
- Safety considerations
- Tool and equipment preparation
Foundation Requirements and Preparation
The foundation is critical for proper machine operation and longevity. Essential elements include:
1. Concrete Foundation Specifications:
- Minimum concrete strength: 3000 PSI
- Foundation depth: 12-24 inches
- Reinforcement requirements
- Leveling provisions
- Vibration isolation
2. Site Preparation Checklist:
- Ground compaction testing
- Moisture barrier installation
- Rebar placement
- Anchor bolt positioning
- Surface finishing requirements
Machine Positioning and Alignment
Proper positioning ensures optimal performance and safety:
1. Equipment Required:
- Industrial crane or forklift
- Precision levels
- Laser alignment tools
- Shims and leveling plates
- Torque wrenches
2. Alignment Steps:
- Initial positioning
- Level checking
- Roll alignment verification
- Gap adjustment
- Parallelism confirmation
Electrical and Hydraulic Systems Setup
The integration of power and hydraulic systems requires careful attention:
1. Electrical Installation:
- Power supply verification
- Control panel mounting
- Wiring connections
- Emergency stop system
- Safety interlock setup
2. Hydraulic System:
- Oil tank filling
- Pressure testing
- Leak checking
- Filter installation
- Temperature monitoring setup
What are the basic requirements for installing a 3-roll plate bending machine?
The basic requirements include adequate foundation strength, proper power supply, sufficient space for operation and maintenance, and appropriate environmental conditions.
How long does the installation process typically take?
A standard installation typically takes 2-5 days, depending on site preparation, machine size, and complexity of the setup.
What are the power requirements for a typical 3-roll plate bending machine?
Power requirements vary by model but typically range from 30-100 kW, with 3-phase power supply being standard.
How important is foundation preparation?
Foundation preparation is critical as it affects:
- Machine stability
- Operating precision
- Vibration control
- Long-term reliability
- Safety considerations
What safety features should be installed?
Essential safety features include:
- Emergency stop systems
- Safety guards
- Warning signals
- Light curtains
- Safety interlocks
How often should alignment be checked after installation?
Initial alignment should be checked:
- After first 24 hours of operation
- Weekly for the first month
- Monthly thereafter
- After any significant vibration events
What maintenance is required post-installation?
Regular maintenance includes:
- Alignment checks
- Hydraulic fluid monitoring
- Bearing inspection
- Control system testing
- Safety system verification
How do you verify proper installation?
Verification includes:
- Test runs with various materials
- Measuring bend accuracy
- Checking hydraulic pressures
- Verifying safety systems
- Documenting alignment readings
What tools are needed for installation?
Essential tools include:
- Precision levels
- Alignment lasers
- Torque wrenches
- Hydraulic tools
- Measuring instruments
How do you prepare for potential issues during installation?
Preparation should include:
- Backup power plans
- Spare parts inventory
- Technical support contacts
- Contingency procedures
- Emergency response plans
Key Installation Steps:
1. Site preparation
2. Foundation construction
3. Machine positioning
4. Alignment and leveling
5. Systems connection
6. Testing and verification
7. Operator training
Critical Features to Verify:
- Roll parallelism
- Hydraulic pressure settings
- Control system operation
- Safety system functionality
- Material handling clearances
https://www.hualuforgingmachine.com
-
1:02:38
Donald Trump Jr.
7 hours agoNew Year’s Terror, Latest Breaking News with Sebastian Gorka | TRIGGERED Ep.204
103K201 -
59:59
The StoneZONE with Roger Stone
2 hours agoAfter Years of Targeting Trump, FBI and DOJ are Unprepared to Stop Terror Attacks | The StoneZONE
5.52K2 -
LIVE
Leonardaisfunny
44 minutes agoH-1b Visas: Infinity Indians
543 watching -
LIVE
Josh Pate's College Football Show
5 hours ago $0.07 earnedPlayoff Reaction Special: Ohio State Owns Oregon | Texas Survives | UGA vs Notre Dame Takeaways
123 watching -
58:04
Kimberly Guilfoyle
5 hours agoFBI's Terror Response Failures, Live with Steve Friend & Kyle Seraphin | Ep. 185
76.9K35 -
2:15:01
WeAreChange
6 hours agoMassive Developments In Vegas Investigation! UNREAL DETONATION, Shocking Details Emerge!
76.1K20 -
54:02
LFA TV
12 hours ago2025 Is Off to a Violent Start | TRUMPET DAILY 1.2.25 7pm
18K1 -
59:27
theDaily302
11 hours agoThe Daily 302- JJ Carrell
20.3K2 -
2:57
EvenOut
1 day ago $1.28 earnedTHE TELEPORTING PORTA POTTY TWIN RPANK!
23K -
1:02:55
In The Litter Box w/ Jewels & Catturd
1 day agoAmerica Is Under Attack! | In the Litter Box w/ Jewels & Catturd – Ep. 711 – 1/02/2025
88.1K113