Premium Only Content
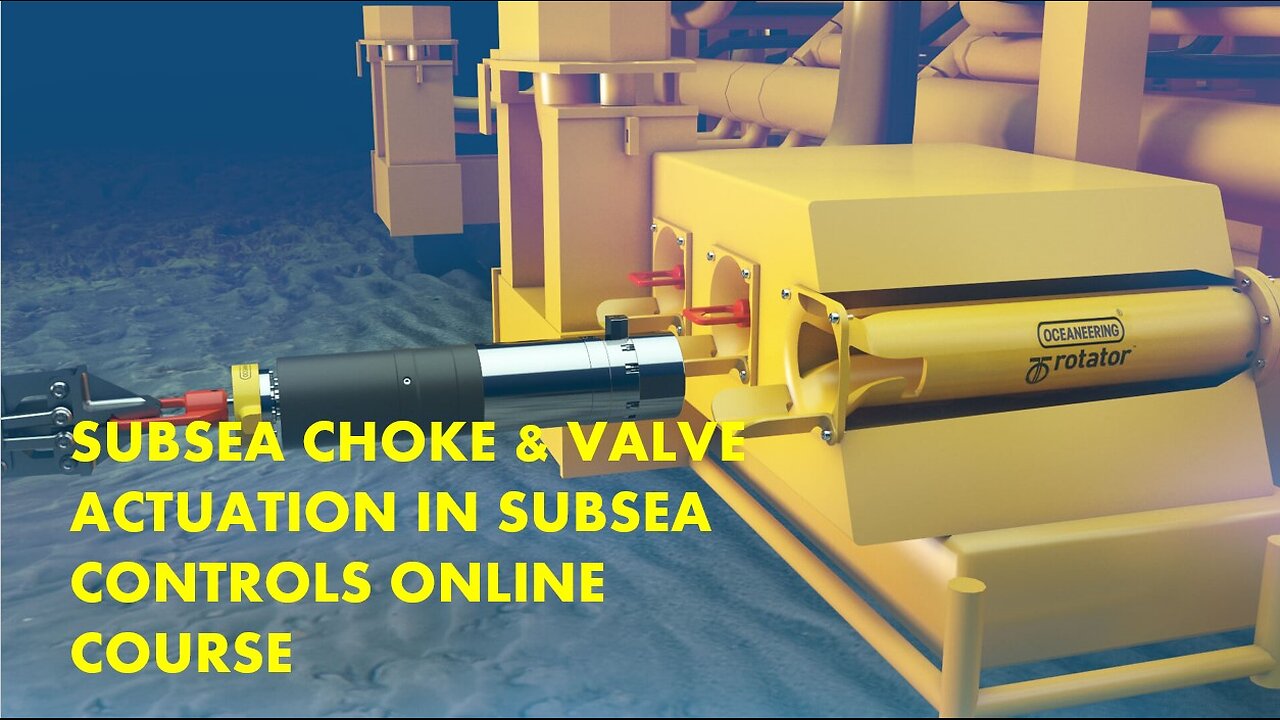
Subsea Choke & Valve Actuation Online Course
Choke application
The choke valve is used to commingle the production subsea from wells with different pressure to reduce the number of flowline and risers. Subsea chokes may also be required to fulfill gas lift and water injection functions. Two types of choke valves exist—a fixed or rotating disc, single-stage choke valve and a plug type single-stage choke valve. These valves must be easy to replace either by a remotely operated vehicle (ROV) or a remote-operated tool (ROT).
Hydraulic versus electric
Traditional electro-hydraulic chokes rely on stepping actuators. Each stepping actuator requires two hydraulic control valves and roughly 200 to 250 steps to go from the fully closed to fully open position. ROV-operated chokes cannot be adjusted based on production of the individual wells as frequently as operators would like. The electric choke can be easily integrated to a hydraulic or electric control system. It is driven by a motor and does not require stepping, therefore enabling greater control and precision.
All-electric control is simpler and more cost efficient than a conventional electrohydraulic system. Electrically actuated chokes provide several advantages during production startup and shutdown. An infinite number of precise positioning means that wells can be brought onstream and shut down gradually to prevent formation damage. There is also an improved response time in diagnostics and interpretation of measurements coming from the downhole valves, sensors, wellhead, and subsea instrumentation.
For full videos you can visit this link :
https://drive.google.com/file/d/1FGpuDrInRkkueauuso39xVpErS8B7o25/view?usp=sharing
and you will be directed to a google drive link where you can download all files of this course
https://drive.google.com/file/d/1pb_6F_friRGAH04X-6T6iOfesWbZbZm-/view?usp=drive_link
-
LIVE
Joe Donuts Live
1 hour ago🟢LIVE : Skyscraper Blues | Verdansk With The Squad!
50 watching -
LIVE
Dorian_D
11 hours ago🔴Dorian's Magical First Adventure: Hogwarts Legacy Playthrough
663 watching -
46:03
SouthernbelleReacts
3 days ago $5.18 earnedShutter Island Reaction | I Did NOT See That Ending Coming! | SouthernBelle Reacts
24.2K6 -
6:39
nospeedlimitgermany
2 days ago $4.03 earnedBMW M3 E46 | 343 PS | Top Speed Drive German Autobahn No Speed Limit POV
26.5K9 -
LIVE
tylerpasta
3 hours ago🔥 Lock ‘n Load with TylerPasta – Warzone Wins & Pasta Power! 🍝💥
79 watching -
11:41
Sideserf Cake Studio
23 hours ago $3.41 earnedI Made A Disco Ball Cake!
32K9 -
4:58:51
Steven Crowder
17 hours agoLIVE: No Kings Day - Following The Money w/ Guest: Data Republican | Louder with Crowder
834K445 -
1:11:45
Man in America
15 hours ago🚨 America Descends Into CHAOS—Are You Prepared?
87.9K79 -
2:23:54
Badlands Media
1 day agoDevolution Power Hour Ep. 363: Lawfare, Psyops, and the Great Narrative Reversal
113K38 -
2:32:48
Tundra Tactical
10 hours ago $10.88 earnedSilencers, Senators, and Survival: Roasting Lies and a Security Breakdown of The MN Shooting
68.4K8