Premium Only Content
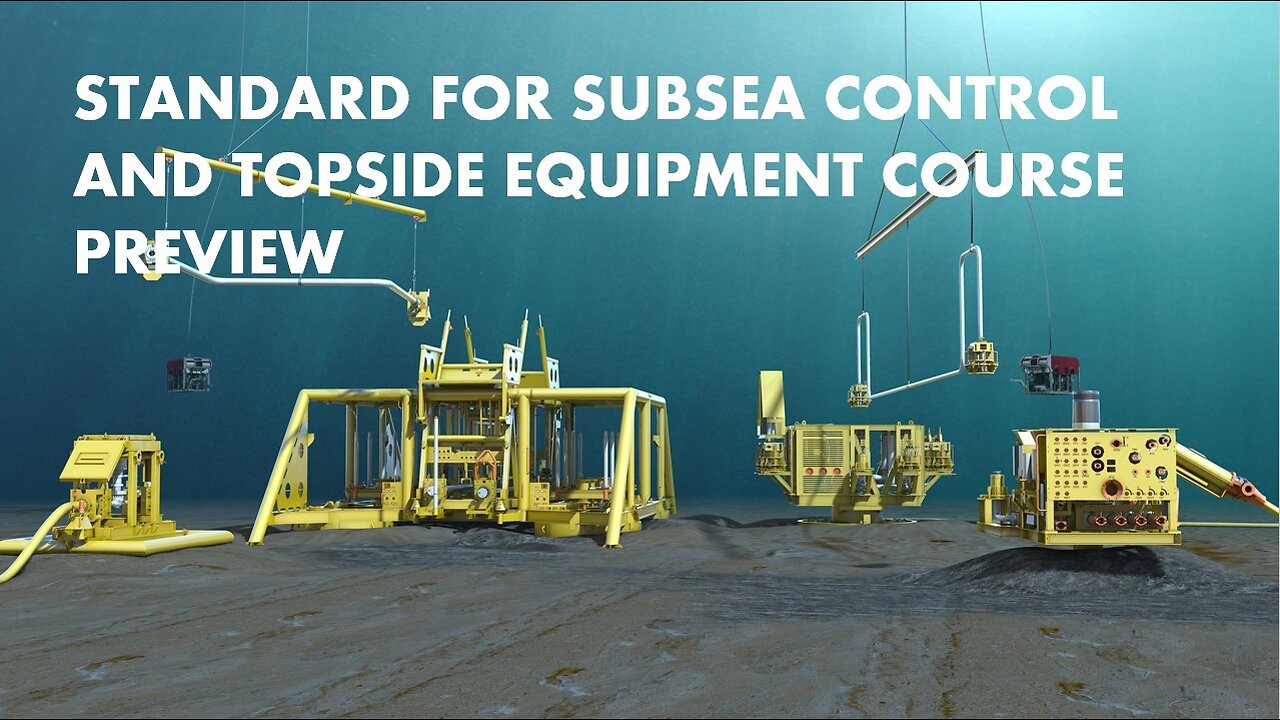
Standards for Subsea Control and Topside Equipment Online Course
Subsea control system architectural concepts can be designed to increase reliability and availability. Failure of a single subsea electronic module (SEM) does not have to shut down production nor does it have to reduce the safety integrity level (SIL) of the system. If repair is delayed due to weather or lack of surface-support equipment availability, subsea production can remain operational indefinitely.
Earlier subsea production control and safety systems were mounted primarily topside, with communication links to I/O installed subsea. The nature of these installations has evolved as more processes have moved underwater. Gas/liquid separation, pumping, and subsea compression require high-speed response, so closed-loop control cannot be accomplished with the communication delays inherent with topside mounting. This need for speed has helped delay the use of subsea applications requiring these features. A number of issues must be resolved before a more autonomous subsea control and safety system can be deployed.
All the architectures presented can provide SIL2 or SIL3 coverage. The challenge is to adapt topside technology for subsea use. Subsea control and safety systems are housed in SEMs, which maintain a nitrogen atmosphere for the electronic components. Space is at a premium in SEMs and electrical wiring penetrations to the module are expensive. The redundant field devices required to achieve a certain SIL rating doubles the number of wires and vessel penetrations.
For full videos you can visit this link :
https://drive.google.com/file/d/1S6aw-J0bRLhSWp_l4C8kRyxKQFkiAbGj/view?usp=sharing
and you will be directed to a google drive link where you can download all files of this course
https://drive.google.com/file/d/1CmJhCuxAO0ItlrQyqvlvfd8WJsmcMLuH/view?usp=drive_link
-
LIVE
ttvglamourx
43 minutes agoPLAYING WITH VIEWERS !DISCORD
85 watching -
LIVE
VapinGamers
1 hour agoTools of the Trade - Of Thumbnails and Titles, What's Important? - !rumbot !music
85 watching -
52:11
X22 Report
2 hours agoMr & Mrs X - [DS] Trafficking Empire – How Epstein Built His Web of Wealth and Deceit:Part 1 - Ep 5
58.1K10 -
1:13:18
Wendy Bell Radio
6 hours agoPet Talk With The Pet Doc
34.3K57 -
LIVE
dieseldesigns
5 hours agoExploring Labs In the DARK! // Abiotic factor
12 watching -
LIVE
BBQPenguin_
4 hours agoDragonball Z - The Android Saga
187 watching -
LIVE
Total Horse Channel
4 hours ago2025 URCHA Futurity | Derby & Horse Show | Saturday
44 watching -
LIVE
DynastyXL
4 hours ago🔴LIVE: Fortnite The Comeback Stream Starts Here🎃
46 watching -
1:38:57
njgaming23
2 hours agoCoffee and Morning vibes #rumbletakeover
6.33K -
1:09:19
Ami's House
2 days ago $14.96 earnedWhen Defending Israel Backfires: Are We Pushing Our Last Friends Away? With Karys Rhea
177K183