Premium Only Content
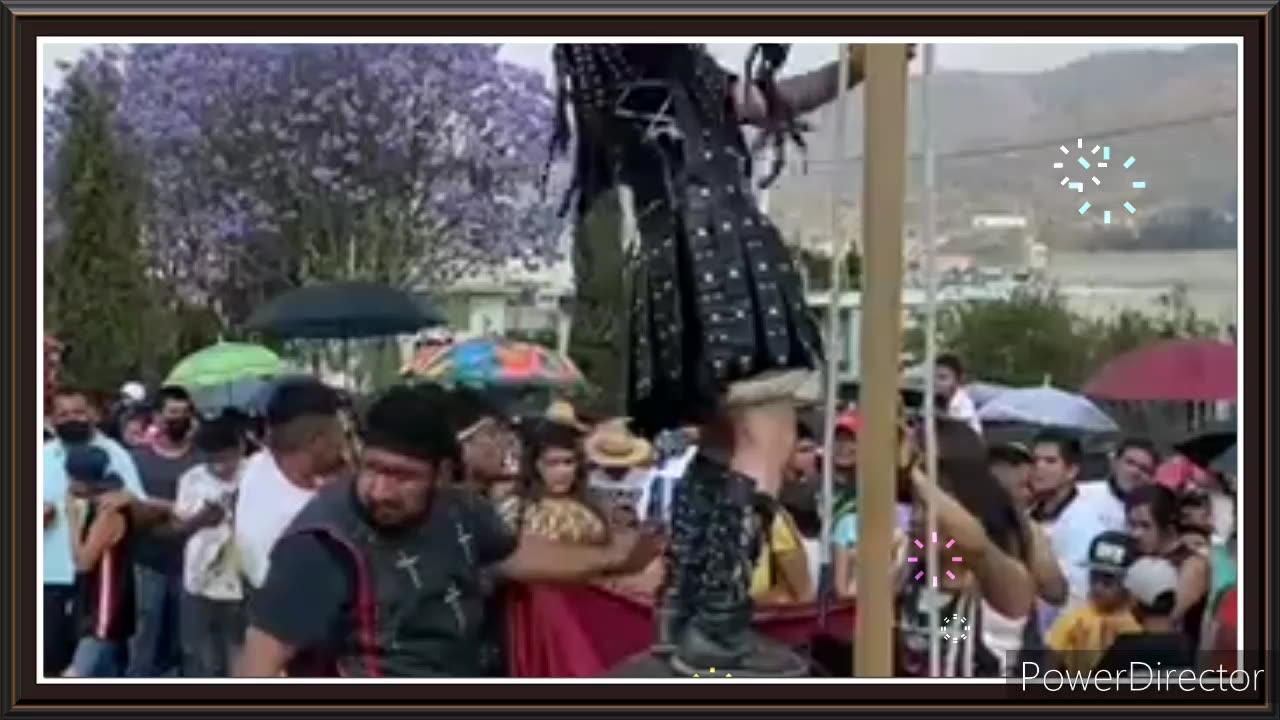
How May Channal Rumbal khoubsoort videos AlliAbbase the morning and get home
۔
'' If That's Ahmad Us Mani '' bought burj khalifa ticket (47k).
The world boasts numerous tall buildings, including the renowned 830-meter Burj Khalifa. Additionally, plans exist for buildings that will surpass even this iconic structure. While these buildings may appear fascinating, have you considered their purpose and why everyone seeks to build them? Furthermore, how long will this race continue and what height is the limit?
In June 2010, Burj Khalifa was the recipient of the 2010 "Best Tall Building Middle East & Africa" award by the Council on Tall Buildings and Urban Habitat.[157] On 28 September 2010 Burj Khalifa won the award for the best project of the year at the Middle East Architect Awards 2010.[158] Awards Chair Gordon Gill, of Adrian Smith + Gordon Gill
March 2008
The tower was constructed by Samsung C&T from South Korea, which also did work on the Petro As Twin Towers and Taipei 101.[85] Samsung C&T built the tower in a joint venture with Besides from Belgium and Arabic from the UAE.[86][87] Turner was the project manager on the main construction contract.[88] Hong Kong-based Far East Aluminum combined to provide the exterior cladding for Burj Khalifa.[89][90]
The contractor and the engineer of record was Hyder Consulting.[91] Under UAE law, the contractor and the engineer of record is jointly and severally liable for the performance of Burj Khalifa.
The primary structure is reinforced concrete. Put Meister created a new, super high-pressure trailer concrete pump, the BSA 14000 Ship-to-shore, for this project.[23] Burj Khalifa's construction used 330,000 m3 (431,600 cu yd) of concrete and 55,000 tonnes (61,000 short tons; 54,000 long tons) of steel rebar, and construction took 22 million man-hours.[13] In May 2008 Puts Meister pumped concrete with more than 21 MPA ultimate compressive strength of gravel to surpass the 600 meters weight of the effective area of each column from the foundation to the next fourth level, and the rest was by metal columns jacketed or covered with concrete to a then world record delivery height of 606 m (1,988 ft),[23] the 156th floor. Three tower cranes were used during the construction of the uppermost levels, each capable of lifting a 25-tonne load.[92] The remaining structure above was constructed of lighter steel.
In 2003, 33 test holes were drilled to study the strength of the bedrock underlying the structure. "Weak to very weak sandstone and siltstone" was found, just metres below the surface.[citation needed] Samples were taken from test holes drilled to a depth of 140 metres, finding weak to very weak rock all the way.The study described the site as part of a "seismically active area".[citation needed] Another challenging element was the shamal which often creates sandstorms.
Over 45,000 m3 (58,900 cu yd) of concrete, weighing more than 110,000 tonnes (120,000 short tons; 110,000 long tons) were used to construct the concrete and steel foundation, which features 192 piles; each pile is 1.5 metre in diameter by 43 m in length, buried more than 50 m (164 ft) deep.The foundation was designed to support the total building weight of approximately 450,000 tonnes (500,000 short tons; 440,000 long tons). This weight was then divided by the compressive strength of concrete which is 30 MPa which yielded 450 sq. meters of vertical normal effective area, which then yielded 12 meters by 12 meters dimensions.[95] A cathodic protection system is under the concrete to neutralize the sulphate and chloride-rich groundwater and prevent corrosion.
During the construction of the Burj Khalifa, over 35,000 tonnes of structural steel which held the Palace of the Republic, the former parliament building of the German Democratic Republic, the Volkswagen, in East Berlin together were shipped to Dubai in 2008.
The Burj Khalifa is highly compartmentalized. Pressurized, air-conditioned refuge floors are located every 13 floors (on floors G, 13, 26, 39, 52, etc.) where people can shelter on their long walk down to safety in case of an emergency or fire.
Special mixes of concrete were made to withstand the extreme pressures of the massive building weight; as is typical with reinforced concrete construction, each batch of concrete was tested to ensure it could withstand certain pressures. CTL Group, working for Skidmore, Owings and Merrill, conducted the creep and shrinkage testing critical for the structural analysis of the building.
The consistency of the concrete used in the project was essential. It was difficult to create a concrete that could withstand both the thousands of tonnes bearing down on it and Persian Gulf temperatures that can reach 50 °C (122 °F). To combat this problem, the concrete was not poured during the day. Instead, during the summer months, ice was added to the mixture and it was poured at night when the air was
-
LIVE
Illyes Jr Gaming
2 hours agoBack to Black .....Ops 6 w/ ILLYESJRGAMING
74 watching -
1:07:59
BonginoReport
5 hours agoBoston Mayor Defies Trump, Protects Illegals - Nightly Scroll w/ Hayley Caronia (Ep.115)
98.4K69 -
40:45
Donald Trump Jr.
6 hours agoPeace by Peace: Solving One Problem After Another | Triggered Ep.268
52.1K54 -
LIVE
FrizzleMcDizzle
3 hours ago $0.43 earnedRemnant 2 - Dark Souls-like Shooter?!
144 watching -
LIVE
FoeDubb
1 hour ago🏰KINGDOM MENU: 🏈FOOSBALL & 🎮DELTA FORCE PEW PEWS DILLY DILLY!!
21 watching -
11:43:31
GritsGG
13 hours agoWin Streaking! Most Wins 3390+ 🧠
60.9K -
1:08:29
TheCrucible
5 hours agoThe Extravaganza! Ep. 24 (8/19/25)
79.3K18 -
4:22:25
sophiesnazz
6 hours ago $0.83 earnedLETS TALK ABOUT BO7 !socials !specs
19.1K -
1:27:30
Redacted News
6 hours ago"There will be consequences!!!" Trump issues big threat to Putin ahead of peace summit | Redacted
104K174 -
Amish Zaku
4 hours agoWar Thunder - Tank Tuesday - then Peak
14.9K1