Premium Only Content
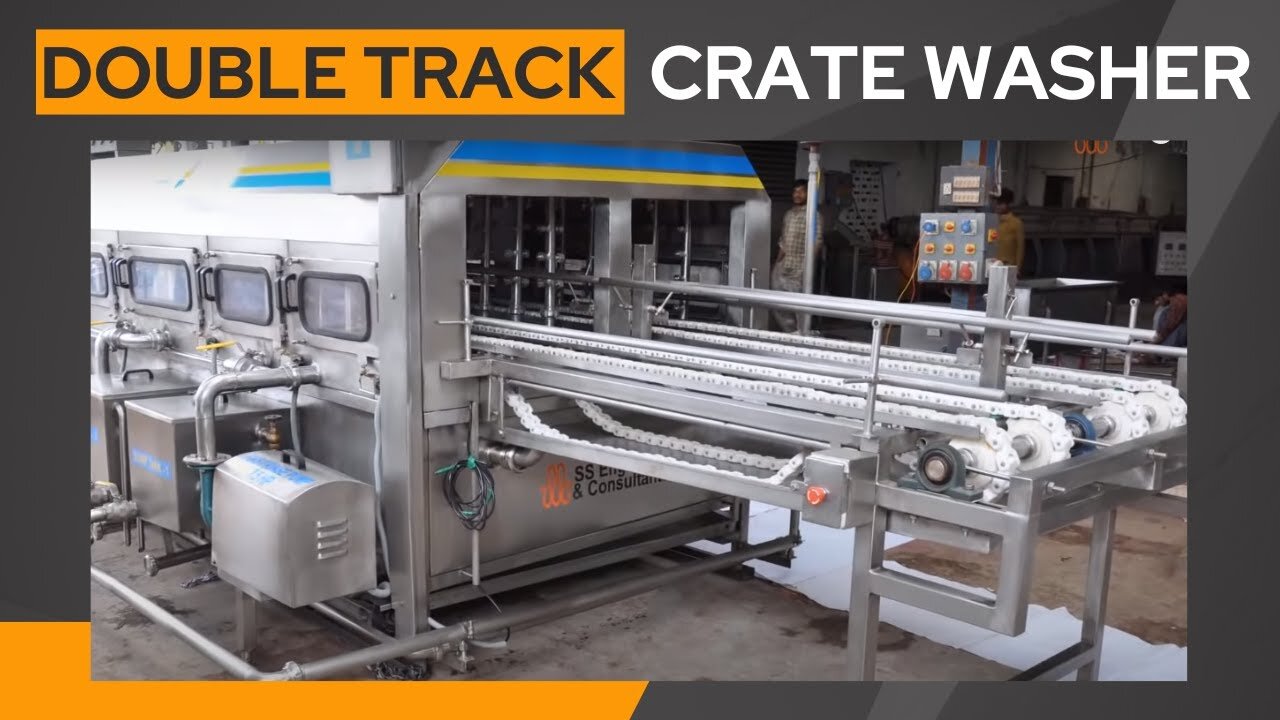
Double Track Crate Washer | Hatchery Basket Washer | Chick Basket Washer
Please click the below links for more details: 👇
Product Link: https://ssengrindia.com/ln/ig/crate%2...
Contact us : https://b24-jupuge1.bitrix24.site/crm...
#DoubleTrackCrateWasher #CrateWashing #PoultryEquipment #HatcheryBasketWasher #ChickBasketWasher
In industries that rely on efficient cleaning and sterilization of crates, the double-track crate washer plays a vital role. This innovative machine is designed to streamline and automate the crate washing process, ensuring cleanliness and hygiene in various sectors such as food and beverage, agriculture, logistics, and more.
Step 1: Loading the Crates:
The first step in the process involves loading the dirty crates onto the double-track conveyor system. These crates may contain residue, debris, or other contaminants. The conveyor system efficiently transports the crates through the washer, allowing for continuous cleaning and maximizing productivity.
Step 2: Pre-Washing:
Once the crates are loaded onto the conveyor, they pass through the pre-washing stage. High-pressure water jets or nozzles are strategically positioned to remove larger particles and loose debris from the crates. This initial rinse prepares the crates for thorough cleaning in subsequent stages.
Step 3: Main Washing:
After pre-washing, the crates move into the main washing section of the machine. Here, powerful jets of hot water mixed with a detergent solution are sprayed onto the crates from multiple angles. The combination of heat, water pressure, and detergent effectively removes stubborn stains, grease, and contaminants from the crate surfaces. This stage ensures a thorough and hygienic cleaning process.
Step 4: Intensive Scrubbing (Optional):
In some double-track crate washers, an optional intensive scrubbing stage can be incorporated. This step employs rotating brushes or scrubbers to provide an extra level of cleaning for crates with stubborn residue. The brushes reach into corners and crevices, ensuring a deep and thorough clean.
Step 5: Rinse Cycle:
Following the main washing and optional scrubbing stages, the crates undergo a rinse cycle. High-pressure water jets rinse off any remaining detergent, debris, or particles from the crate surfaces. This step is crucial to achieve a residue-free and sanitized result.
Step 6: Optional Disinfection:
For industries with stringent hygiene requirements, an optional disinfection stage can be included in the double-track crate washer. This stage involves the application of a sanitizing solution or steam jets to eliminate bacteria, pathogens, and other microorganisms, ensuring the crates are properly sterilized.
Step 7: Drying:
After the cleaning and disinfection process, the crates move to the drying section of the machine. Various drying methods can be employed, such as hot air blowers or air knives, to effectively remove excess moisture from the crate surfaces. This ensures that the crates are ready for immediate use or storage without the risk of bacterial growth or contamination.
Step 8: Unloading:
Once the crates are thoroughly cleaned, sanitized, and dried, they are automatically unloaded from the double-track crate washer. The clean crates can then be directed to the next stage of production or safely stored until they are needed.
If you like this video, please share it on your page making it reach the actual user.
👉 YouTube:
https://www.youtube.com/c/SSEngineersConsultants
👉 LinkedIn:
https://www.linkedin.com/company/ssengineersandconsultantspvtltd/mycompany/
👉 Twitter:
https://twitter.com/ssengrindia
👉 Facebook:
https://www.facebook.com/ssengineersandconsultantspvtltd
👉Website: https://www.ssengrindia.com
Contact us:
👇
SS ENGINEERS & CONSULTANTS
#11-49, Morampudi Junction, Rajahmundry - 533107, Andhra Pradesh, INDIA.
Ph: (+91) 93979 16115, (+91) 98514 46644, (+91) 883 2426845, 46
E-mail: response.ssengrindia@gmail.com
-
LIVE
Lofi Girl
2 years agoSynthwave Radio 🌌 - beats to chill/game to
271 watching -
2:21:40
FreshandFit
7 hours agoOF Bimbo Gets TRIGGERED Over Systemic Racism! HEATED DEBATE
87.6K74 -
2:03:03
Inverted World Live
11 hours agoPregnant Robots | Ep. 93
117K22 -
LIVE
Akademiks
6 hours agoDrake vs Roc Nation! Tory Lanez argues for new Trial! Bloodhound Q50 dodged 60 shots.
1,271 watching -
1:58:16
Badlands Media
22 hours agoBaseless Conspiracies Ep. 146: GART Deadwood Highlights
83.9K24 -
4:55:43
Drew Hernandez
14 hours agoTRUMP SECURES SETTING MEET BETWEEN PUTIN & ZELENSKYY
27.4K11 -
5:06:26
SpartakusLIVE
10 hours agoSpartan HERO here to MOTIVATE the MASSES
58.5K2 -
1:27:19
Badlands Media
22 hours agoCulture of Change Ep. 117: DARPA, Downloads & the Roots of the Narrative
67.8K9 -
LIVE
BubbaSZN
18 hours ago🔴 LIVE - MAFIATHON (COMPLETING THE MAFIA SERIES WITHOUT ENDING STREAM)
386 watching -
2:50:02
TimcastIRL
9 hours agoTrump Calls Putin During Zelenskyy White House Visit, European Leaders Praise Trump | Timcast IRL
199K69