Premium Only Content
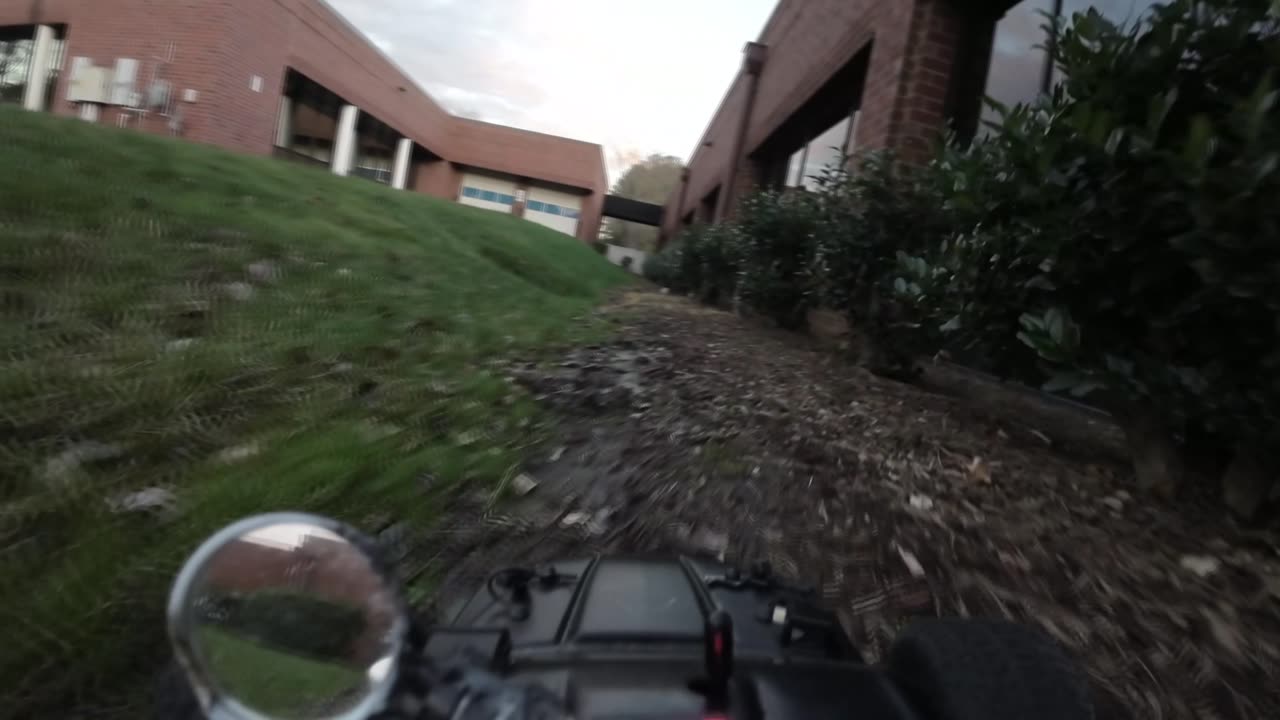
Big Rock 3s FPV Sensored ESC/Motor 2400Kv Quick Test
This is using a Copperhead 10 ESC and Hobbywing 2400kv motor with stock gearing. I first tried the 2400kv motor with the Hobbywing Max10 G2 140A ESC it came with but somehow burned out that ESC in minutes. I was thinking the Copperhead might burn out too so I drove around close range for a while and creeped with it. So far it's worked fine but I still liked the Hobbywing better while it lasted. The weight of my Big Rock is probably at the upper limit of what the ESC/motor can move around so I still wouldn't try to put bigger tires on it unless I can find like an 11 tooth pinion.
The point of the sensored setup for me was to mainly avoid cogging but to also allow me some ability to power through resistance from a dead stop. With the stock gearing and 3200Kv motor the Big Rock can power through a lot of stuff no problem, but if you were to catch it at a dead stop in just the right amount of resistance it might just sit there and cog. This setup keeping the stock 15t pinion seems to work where I still have decent top speed and have a lot more low speed torque than I did before.
Cogging is basically when a sensorless setup is trying to locate a particular orientation of the windings relative to the magnets. Since there is no precise feedback it has to deliver a ton of current to try to get the rotor moving in order to 'find itself' and then engage proper driving rotation. This is why repeatedly cogging the motor through a heavy resistance is creating high currents in the system.
The sensored combination is able to allow the ESC to keep a low current feedback loop at any time so it's always able to start a real smooth but powerful creep from a dead stop. This means that if I'm far away and find myself stuck in some tall grass or other obstruction, there's a good chance I can just power over it like a rock crawler would, keeping in mind that I shouldn't try to overdo how much current that might be consuming at the time. With a sensorless setup in such a situation my best hope would be to somehow jolt the throttle into a full blast in order to get the wheels moving and maybe manage to torque out at high rpms. If the wheels are just too deadlocked then a sensorless setup is hopeless.
The Hobbywing Max10 G2 140A ESC is much more substantial feeling than the Copperhead. I don't know how I killed it but for reference I just had it running for a few minutes. It seemed fine and I was really liking it. Then I decided to drive it slowly over a pile of clothes just to demonstrate the torque. At a certain point it just stopped, beeped, then the fan came on. I thought it went into some thermal shutdown so I just let the fan run. The fan eventually shut off but I could never get throttle back. Cycling power caused the fan to come on for a second then stop. I noticed the ESC never did cool down so there was a constant load in it somewhere aside from the control power. Right after I did a factory reset on it the smoothing capacitors spewed out. The BEC/servos never stopped working but any throttle movement just caused it to reset itself. Since I've already driven the Copperhead around more without any issues I just assume it was a random fluke with the Hobbywing.. but it also could have been the combined weight and initial torque allowance of the default settings just being too much of a surge on the switches due to just the right wheel resistance at the time. IDK how to avoid that with a sensored combo unless there is a setting to reduce the initial throttle torque.
-
30:09
Afshin Rattansi's Going Underground
1 day agoCurtis Yarvin: ‘Trump 47 is 10x More Powerful than Trump 45’ & the TOXIC US-Israel Relationship
24.1K34 -
LIVE
Drew Hernandez
9 hours agoTRUMP HINTS DEMS COULD HAVE PLANTED FAKE EVIDENCE & MANIPULATED EPSTEIN FILES
1,047 watching -
LIVE
Eternal_Spartan
12 hours agoThe Legend of Zelda: Majoras Mask Ep. 5 | USMC Vet | Come Join the Best Chat on Rumble!!!!
100 watching -
3:44:24
Barry Cunningham
6 hours agoBREAKING NEWS: LIVE COVERAGE OF NEW YORK POLICE OFFICERS UNDER SIEGE!
88.9K65 -
2:51:25
The Pascal Show
4 hours ago $1.71 earnedBREAKING! Active Shooter In Midtown Manhattan NYC Multiple People Shot!
19.3K2 -
10:25
MattMorseTV
9 hours ago $11.42 earnedVance just DROPPED a NUKE.
38.8K41 -
LIVE
Jokeuhl Gaming and Chat
7 hours agoDARKTIDE - Warhammer 40k w/ Nubes and AoA
197 watching -
2:53:08
Shoriantrax
3 hours agoLIVE: Hardcore Chaos in Tarkov – Loot, Die, Repeat!
10.3K -
LIVE
John_Goetz
4 hours agoJohn Gets Gaming - Medal of Honor Vanguard Part 2
8 watching -
1:29:09
RiftTV
5 hours agoSydney Sweeney Spreading RACIST Propaganda? | The Rift | Guest: Braeden Sorbo + Sarah Stock
38.9K10