Premium Only Content
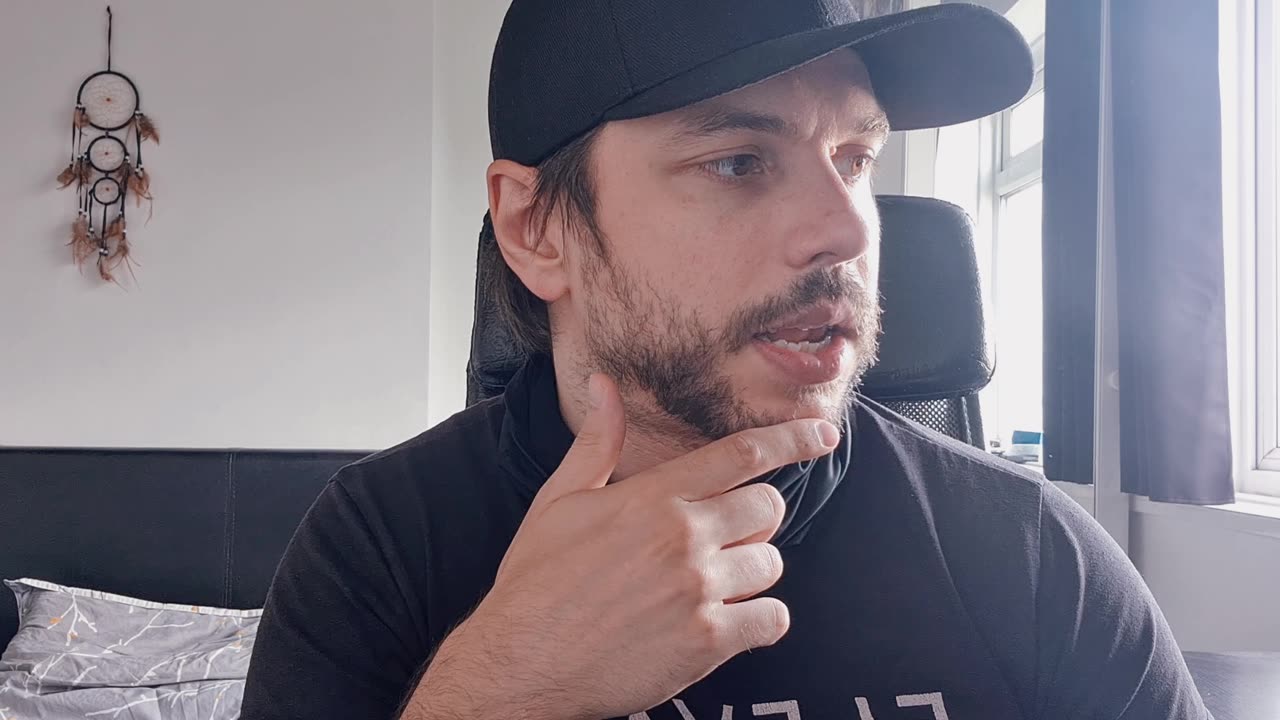
#154 Directed Energy Deposition (DED)
Directed Energy Deposition (DED) is an additive manufacturing (AM) or 3D printing technology used to create complex metal parts and components. It is also known as Laser Metal Deposition (LMD), Laser Cladding, or Laser Metal Additive Manufacturing (LAM). DED is a versatile and precise manufacturing process that involves the following key elements:
Material Feedstock: DED uses a feedstock material in the form of powder or wire. This material is typically a metal alloy. The feedstock is directed towards the build area.
Energy Source: An energy source, often a high-power laser or electron beam, is used to melt the feedstock material. The energy source is precisely controlled and directed to the desired location.
3D Printing Head: The 3D printing head combines the feedstock material with the energy source to create a molten pool. It can move in multiple axes to deposit material layer by layer, following a predefined 3D digital model.
Build Platform: The build platform supports the growing part and can be adjusted vertically as the part is built layer by layer.
DED offers several advantages:
Complex Geometries: DED can create parts with intricate and complex geometries, making it suitable for aerospace, automotive, and other industries where lightweight and high-performance components are required.
Material Variety: It can work with a wide range of materials, including various metals and metal alloys, which makes it versatile for different applications.
Repair and Cladding: DED can be used for repairing worn or damaged parts (cladding) by adding material to the affected area. This is particularly valuable in industries like oil and gas, where critical components can be refurbished rather than replaced.
Low Waste: Because it's an additive process, DED generates minimal waste compared to traditional subtractive manufacturing methods.
Rapid Prototyping: DED is also used for rapid prototyping, allowing engineers to quickly iterate and test designs.
However, there are some limitations and challenges associated with DED:
Surface Finish: DED parts may require post-processing to achieve the desired surface finish, as they can be rough due to the layer-by-layer deposition.
Heat Management: Managing the heat generated during the process is crucial to prevent distortion and stress in the part being built.
Powder Management: Handling and recycling excess powder can be challenging and costly.
Directed Energy Deposition is a valuable technology that complements other additive manufacturing processes like Selective Laser Melting (SLM) and Fused Deposition Modeling (FDM). Its ability to build large, complex parts and repair critical components has made it an important tool in industries where precision, durability, and customization are essential.
www.antharas.co.uk/ companies website or top book distributors!
#BusinessStrategy
#Entrepreneurship
#Leadership
#Management
#Marketing
#Finance
#Startups
#Innovation
#Sales
#SmallBusiness
#CorporateCulture
#Productivity
#SelfDevelopment
#SuccessStories
#PersonalBranding
#Networking
#Negotiation
#BusinessEthics
#TimeManagement
#GrowthStrategies
#MarketAnalysis
#BusinessPlanning
#FinancialManagement
#HumanResources
#CustomerExperience
#DigitalTransformation
#Ecommerce
#SocialMediaMarketing
#BusinessCommunication
#ChangeManagement
-
14:15
AV
10 months ago#1151 Press release - AUKUS real-time AI trials
182 -
LIVE
StoneMountain64
2 hours agoNew CoD Revealed + WTF is Splitgate 2 Doing
236 watching -
1:00:27
Sean Unpaved
3 hours agoGaines' Battle for Title IX, Pittsburgh's Playoff Push, & Why Chubb Matters in Houston
29.6K1 -
LIVE
Jeff Ahern
1 hour agoMonday Madness with Jeff Ahern
224 watching -
1:20:39
Ben Shapiro
2 hours agoILLEGAL IMMIGRANT RIOTS! TRUMP SENDS IN THE TROOPS!
45.8K32 -
1:58:12
The Charlie Kirk Show
3 hours agoThe Battle of Los Angeles + Simone Biles Bile + The BBB | Sen. Scott, Gaines, Homan | 6.9.25
70K35 -
22:16
CryptoWendyO
2 hours ago $0.11 earnedBITCOIN PUMPING NOW (BULLISH NEWS FOR THESE 4 ALTCOINS)
22K1 -
1:20:48
Simply Bitcoin
4 hours ago $0.14 earnedThe Paper Bitcoin ATTACK JUST ENDED: Price is about to EXPLODE!! [HERE'S WHY] | EP 1262
25.3K2 -
53:35
BitLab Academy
6 hours ago $0.18 earned💥 Bitcoin Signal To Watch | Altcoin Pump Next? Crypto Supercycle Signal!
39.8K1 -
Talk Nerdy Sports - The Ultimate Sports Betting Podcast
2 hours agoAI Locks 🔒 + Stanley Cup Fire🔥 | June 9 Bets You Can’t Miss!!!
15.7K