Premium Only Content
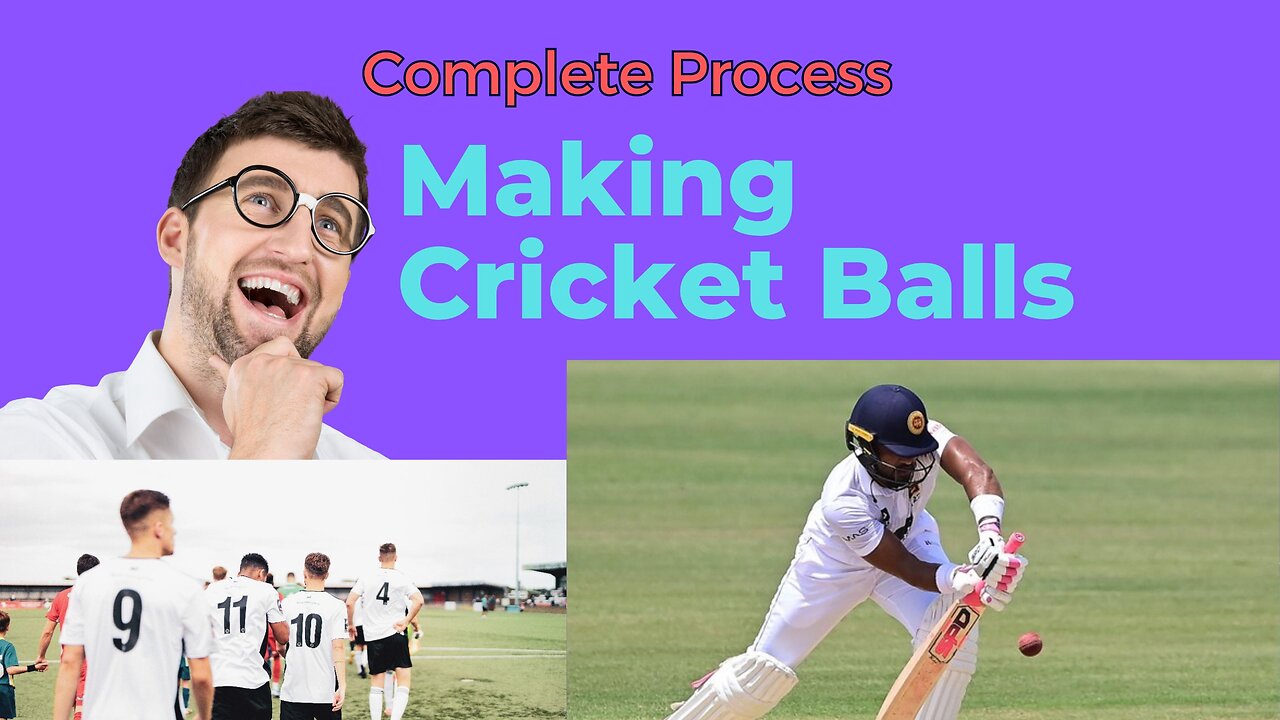
Labored Process of Making Cricket Balls
Complete Process
1) Selection of Raw Materials:
The primary materials used in cricket ball production are leather, cork, and thread. High-quality leather is selected for the outer covering, and cork is chosen for the core.
2) Cutting Leather:
The leather is cut into two identical hemispheres, each forming one half of the ball's outer shell. These pieces will later be stitched together.
3) Shaping Cork Core:
The cork is shaped into a hemisphere that will serve as the core of the cricket ball. It's important to ensure the core is symmetrical and of the correct weight.
4) Stitching:
The two leather hemispheres are stitched together using a specialized technique that ensures the seam remains flush with the surface. This stitching process requires great skill and precision to maintain the ball's shape.
5) Applying Waxed Thread:
The seam is coated with waxed thread to enhance its durability and prevent fraying during play. This also contributes to the ball's ability to swing in the air.
6) Layering and Binding:
Additional layers of cork and string are added to the core to give the ball its structure and weight. The core is bound tightly with string, and another layer of cork is added.
7) Applying Outer Leather:
The core is encased in the two leather hemispheres stitched together earlier. The leather is stretched and glued to ensure a snug fit over the core.
8) Shaping and Pressing:
The ball is carefully shaped using hand tools or specialized machinery to give it its final round and even shape. It is then pressed to compact the materials and solidify the ball's structure.
9) Polishing and Finishing:
The outer surface of the ball is polished to achieve a smooth and consistent texture. This step is crucial for maintaining the ball's aerodynamics during play.
10) Quality Control:
Each ball undergoes rigorous quality control checks to ensure it meets the required weight, dimensions, and performance standards. Balls that pass these checks move on to the next stage.
11) Final Inspection:
A thorough inspection is carried out to detect any defects, inconsistencies, or imperfections. Only balls that meet the strict criteria are approved for use.
12) Stamping and Branding:
The approved cricket balls are stamped with relevant information, such as the manufacturer's logo, ball type (red or white), and any certification marks.
13) Packaging:
The finalized cricket balls are packaged and prepared for distribution. They are usually placed in protective cases or boxes to maintain their condition until they are used in matches.
-
1:09:50
Donald Trump Jr.
8 hours agoHow Sean Parnell Helped Deliver PA, Plus Why Pete Hegseth Must Be Confirmed | TRIGGERED Ep.199
152K75 -
1:58:03
Tucker Carlson
5 hours agoJeffrey Sachs: The Inevitable War With Iran, and Biden’s Attempts to Sabotage Trump
169K267 -
1:31:00
Redacted News
8 hours agoBREAKING! Trump demands answers on UFOs over America as Pentagon hides the truth | Redacted News
172K303 -
1:07:45
BIG NEM
6 hours agoSpiritual STDs, Nikola Tesla & Harnessing Creative Energy! ⚡💡
24.8K1 -
38:09
Patriots With Grit
5 hours agoWe Must Finish This Fight | Glenn Baker
19.6K -
54:52
LFA TV
1 day agoWhy Did God Bring Donald Trump Back to the White House? | Trumpet Daily 12.16.24 7PM EST
36.6K7 -
1:33:00
2 MIKES LIVE
11 hours ago2 MIKES LIVE #156 Author Frank Lasee will Deep Dive into CLIMATE CHANGE!
23.3K1 -
15:36
DeVory Darkins
1 day ago $31.79 earnedGLOVES OFF: Scott Jennings hits CNN Panel with knockout blow
88.5K90 -
28:05
Scammer Payback
13 hours agoHacking the World's Largest Streamer
45.2K5 -
2:16:05
Barry Cunningham
11 hours agoTRUMP DAILY BRIEFING: Can The Trump Train Be Stopped? So Much Winning!
46.6K23