Premium Only Content
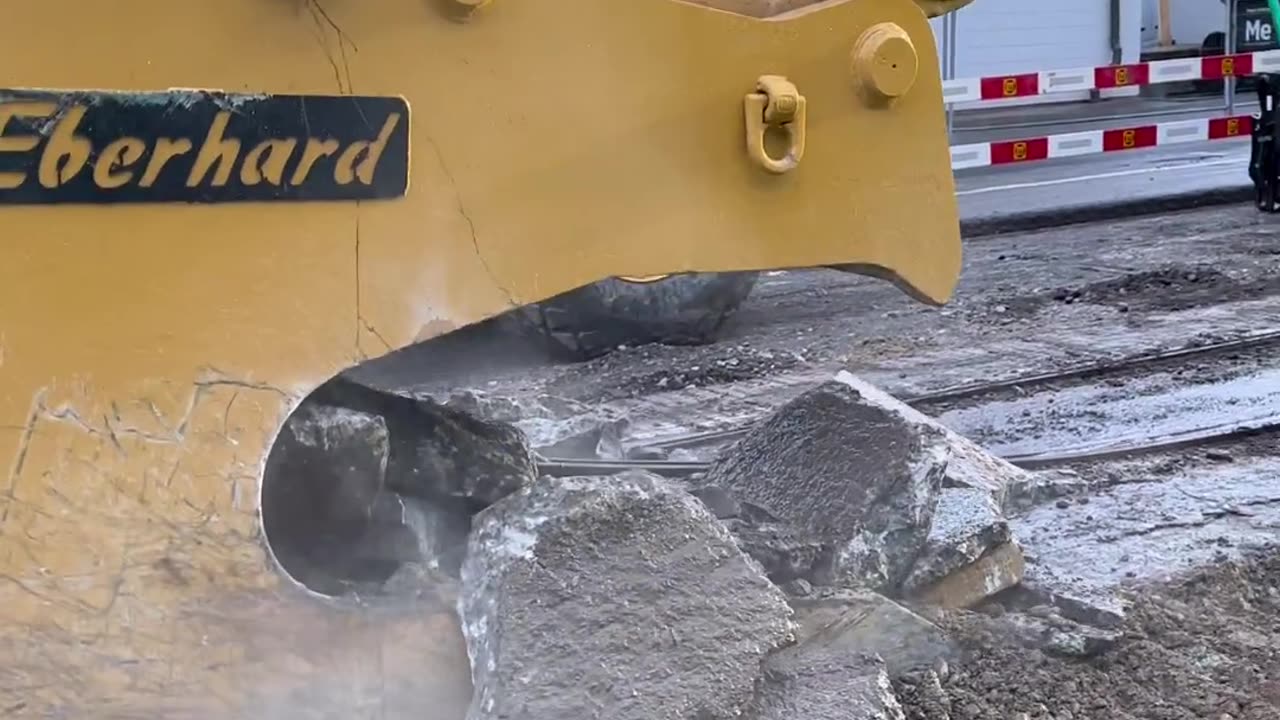
𝐑𝐢𝐩𝐩𝐢𝐧𝐠 𝐨𝐮𝐭 𝐭𝐫𝐚𝐜𝐤𝐬...𝐛𝐢𝐠𝐠𝐞𝐬𝐭 𝐞𝐱𝐜𝐚𝐯𝐚𝐭𝐨𝐫 𝐜𝐫𝐞𝐝𝐢𝐭 𝐭𝐨 : 𝐛𝐢𝐠_𝐦𝐚𝐜𝐡𝐢𝐧𝐞𝐫𝐲
Ripping is a process of breaking up rock and soil with a large tooth or teeth attached to the back of a bulldozer.
Where feasible, ripping is generally preferred over blasting because it is considerably less expensive; ripping costs are typically 50 to 65% less than blasting. Ripping is also significantly less dangerous than blasting and requires fewer permits and special precautions. Ripping can be done in close proximity to populated areas or other places where blasting noise and vibrations are restricted. However, ripping is limited to soft to moderately firm, fractured rock and construction of low-angle cut slopes and shallow, near vertical cuts. In dense rock formations, light blasting is sometimes performed before ripping.
Once the material is loosened by ripping, an excavator can be used to remove it and perform slope sculpting (see below). Ripping gives the contractor a lot of freedom to aesthetically enhance a slope by adding additional contour and allowing for revegetation in certain areas.
The teeth on rippers can leave scar marks on the rock after excavation. In most cases, these can removed using the same procedure used to remove drill hole traces. In soft and/or massive rock, the contractor may use a jet of high-pressure water or a vibratory compactor, known as a plate bucket, which is attached to an excavator or loader to remove the scars.
Ripping is usually done in one direction, but in very tough materials ripping in a grid pattern will increase excavation efficiency. The pass spacing is determined by the end use of the material (fill, aggregate, waste, etc.) and the capacity of the excavating equipment. In most cases, it is best to maximize ripping depth, but in stratified formations it may be best to rip along the natural layers.
Ripping is generally done in the same direction that loading will take place (i.e., parallel to the plane). However, when the material exhibits a foliation or bedding plane, ripping perpendicular to the plane produces much better fracturing.
Ripping Equipment
There are basically two types of rippers: the pull- (or tow-) type ripper and the integral bulldozer- mounted ripper. In rock excavation, a bulldozer-mounted ripper as shown in Figure 21 works better than a pull-type ripper because it can exert greater downward pressure.
Rippers also come in single- and multi-toothed configurations. Single-toothed rippers are used for difficult ripping work, where maximum ripping depth is required and/or the material is dense. Multi-toothed rippers, which can use up to five teeth, are used for softer ground or for secondary purposes such as breaking up already ripped ground.
-
12:53
NC Dirt Hunter
21 hours agoMetal Detecting a Civil War Camp. Both Union and Confederate!
4272 -
18:14
Neil McCoy-Ward
20 hours agoThe European Union Is Getting Worse By The Day… (Now Germany 🇩🇪 Is In Big Trouble)
1.43K5 -
14:06
Gun Owners Of America
15 hours agoTaking A Look At Pam Bondi's Mixed Record On Guns
9832 -
7:44
Tactical Advisor
16 hours agoBest Budget Benelli Shotgun | Orthos v Panzer Arms
1.06K -
6:09
BIG NEM
8 hours agoThe Dark Truth About My Balkan Uncle's Past
6481 -
52:06
Uncommon Sense In Current Times
18 hours ago"Gerrymandering Markets: A Deep Dive with Robert Bork Jr. into Biden's Antitrust Agenda"
853 -
1:02:49
The Tom Renz Show
11 hours agoThe Democrats LA Fires & COVID Grand Jury
1.68K -
47:49
PMG
15 hours ago $0.02 earned"There Ain’t No Grace in It! What to do when you’re worn out!"
1.49K1 -
3:19:06
FreshandFit
6 hours agoAnnoying HOES Kicked Off After HEATED Debate On Rape Culture!
62.1K52 -
57:00
PMG
15 hours ago $10.86 earned"Terror Attacks or False Flags? IT DOESN'T ADD UP!!!"
37.4K12