Premium Only Content
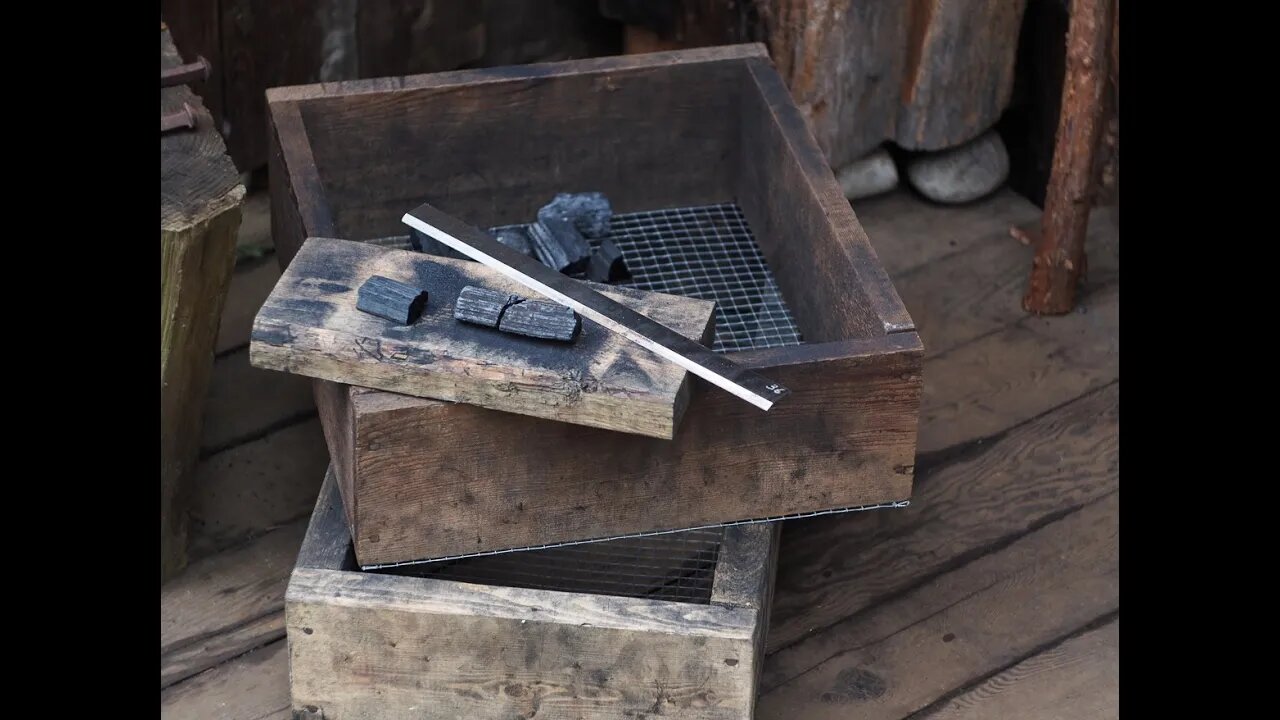
SOTW #4 - Charcoal for Blacksmithing made in a Japanese Style Charcoal Kiln
A quick video shot as we made a batch of charcoal for the forge. We are using a kiln style cooker based on Iwasaki~san's version of a miniature Japanese charcoal kiln. (iwasaki-sumiyaki.com/)
Blacksmithing charcoal must be softwood (bbq charcoal is always hardwood) and we use deadfall pine, mill scrap cedar, and construction scrap from local sources. 97% carbon, charcoal burns much cleaner than mineral coal and is healthier for the 'smith and for the high carbon steel that knives are made of. It is, however, about 1/5th the density of mineral coal which means a lot more shoveling to maintain the forge fire while working.
Charcoal wood is split into small pieces and stacked inside the kiln, then a small fire is started in the combustion chamber. The flue gasses from this fire travel through the stacked wood and "steam" out the water and most of the volatiles at a relatively low temperature. After a couple or three hours, the steam stops and the smoke becomes blue and clear. At this point the kiln is sealed as tightly as possible on all sides to prevent oxygen entering while the charcoal cools overnight. The next day it is opened and the charcoal sorted, chopped, and screened before being stored for use in the forge.
The goal is to create charcoal that is mostly pure carbon but has some of the volatiles left in it. Properly made charcoal is shiny, has a ringing sound, and stays together relatively cleanly. Overcooked charcoal is blown out, crumbly, and very soft. It will still work for most forging, but lacks some of the heat, and loses much volume to dust by the time it is moved around and shoveled into the forge.
One run of the kiln from loading to chopping takes about a day and a half and produces two steel garbage cans full of chopped charcoal, usually enough for a few weeks of our work in the forge (because we do not need to run the forge full time for knifemaking).
Two important notes if you are attempting to use Iwasaki~san's design...
*the wood must be as dry as possible, using wet wood will greatly lengthen the burn time and increase the amount of fuel needed.
**this type of kiln must be insulated to function efficiently, he uses a dry soil mixture and bricks, ours must be portable for now so we are currently using a refractory fibre blanket in the interim (not shown in video)
-
2:21:40
FreshandFit
4 hours agoOF Bimbo Gets TRIGGERED Over Systemic Racism! HEATED DEBATE
33.9K38 -
2:03:03
Inverted World Live
9 hours agoPregnant Robots | Ep. 93
104K19 -
LIVE
Akademiks
4 hours agoDrake vs Roc Nation! Tory Lanez argues for new Trial! Bloodhound Q50 dodged 60 shots.
2,128 watching -
1:58:16
Badlands Media
20 hours agoBaseless Conspiracies Ep. 146
66.9K15 -
Drew Hernandez
11 hours agoTRUMP SECURES SETTING MEET BETWEEN PUTIN & ZELENSKYY
14.3K8 -
5:06:26
SpartakusLIVE
8 hours agoSpartan HERO here to MOTIVATE the MASSES
49.5K1 -
1:27:19
Badlands Media
20 hours agoCulture of Change Ep. 117: DARPA, Downloads & the Roots of the Narrative
52.5K6 -
LIVE
BubbaSZN
16 hours ago🔴 LIVE - MAFIATHON (COMPLETING THE MAFIA SERIES WITHOUT ENDING STREAM)
258 watching -
2:50:02
TimcastIRL
6 hours agoTrump Calls Putin During Zelenskyy White House Visit, European Leaders Praise Trump | Timcast IRL
178K62 -
1:54:34
FreshandFit
11 hours agoBrandon Carter Returns
45.1K6